The 3D-printed homes market is a new way of building houses using 3D-printing technology. This method can help reduce carbon emissions in construction. It works by using automated machines to build houses layer by layer, which can lower costs and make home building faster and more efficient.
Read Brick & Bolt blog to understand more about 3D-printed homes, their construction procedure, pros and cons and real-world examples.
What Are 3D-Printed Homes?
You can understand a 3D-printed house as a residential structure built by 3D printing technology. In this method, a 3D printer will be used to convert your desired blueprint or CAD drawing to construct a physical structure by printing step by step in layer materials. This procedure can be more sustainable and time- and cost-effective compared to regular construction.
3D-printed homes have the following unique characteristics:
Quick Construction—These kinds of homes are constructed way quicker compared to traditional houses.
Lower Costs—3D printed houses cost less, as they require fewer workers and use material efficiently.
Eco-friendly—3D-printing results in less waste during the building process, and some of the materials used are recycled or sustainable.
Unique Designs—This enables unique and tailored house designs that are very difficult to create with normal construction techniques.
How are 3D Printed Homes Constructed?
Commonly, the process of building a 3D-printed house contains the following steps:
Step 1: Digital Design & Blueprinting
The construction of a 3D-printed home always starts with a well-structured digital blueprint. Architects and engineers use Computer-Aided Design (CAD) and Building Information Modeling (BIM) software to create specific models of your dream home. You need to work with them to create a blueprint that accurately suits your specific needs. These digital designs will include the exact dimensions, structure, and layout of the house.
Step 2: On-Site Printing
You need to institute the large-scale robotic 3D printer on-site. These printers, usually gantry-style or robotic arm printers, operate on a track system.
The site where the home is to be printed must be carefully prepared, needing a level, stable surface; in some situations, a foundation is laid ahead of time to distribute the home’s weight. In a layer-by-layer process, the printer adheres to the design it has been programmed with, depositing the concrete mix through a nozzle. Here’s how it works:
- The printer follows the programmed design and moves systematically to create walls and structural components.
- The extruded material hardens quickly, allowing the next layer to be placed without collapsing.
- Reinforcements, such as liquid metal or fiber additives, are sometimes embedded within the layers to enhance durability.
- The process continues until the entire frame of the house is complete.
This method significantly reduces construction time—what traditionally takes weeks can be completed in just a few days.
Step 3: Post-Printing Finishing
After the structure has been printed, you need to install the necessary systems like wiring, plumbing, insulation, and HVAC systems. As they mainly build the walls, conventional construction teams are still required to handle these vital installations. To simplify this step, some 3D printing technologies incorporate pre-designed conduits into the walls so that pipes and wiring can simply be inserted without modification. Most 3D printers are not yet capable of printing roofs, so traditional methods are used to install prefabricated roofs. Similarly, windows, doors, and interior finishes are added manually to complete the house. The home undergoes finishing touches, which may include painting, plastering, flooring, interior decorating work, cabinetry, landscaping, and exterior design.
Materials Used: This technique doesn’t require traditional building materials such as bricks, wood, and steel. 3D printing in construction mainly requires concrete-based materials. The most common materials include:
- Concrete mixtures – Particulary prepared for extrusion and fast setting.
- Geopolymers – More eco-friendly substitutes for cement.
- Clay and recycled materials – Sustainable options earning popularity.
Benefits of 3D-Printed Homes
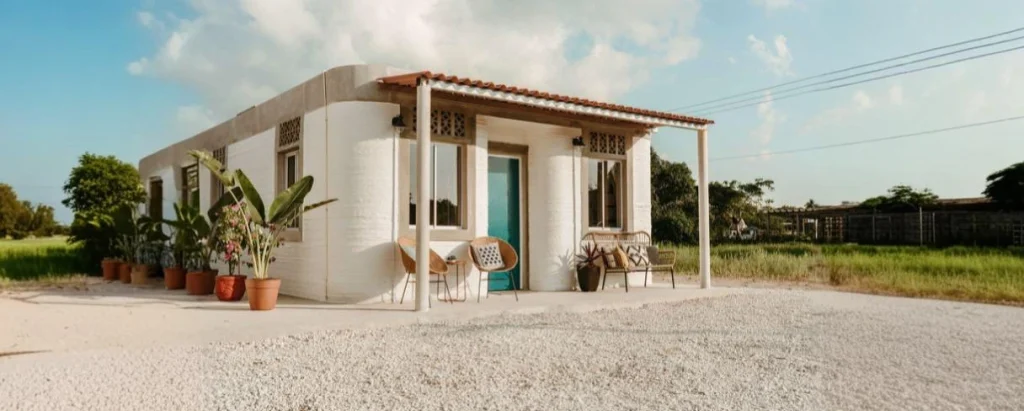
The following are the major benefits of 3D-printed homes:
- Construction Cost: Compared to traditional house construction costs, 3D printed house costs are more affordable (up to 45%). It takes very little labour, reduces labour charges, and optimises material usage. Thus, it saves overall construction cost, making it easy to build more affordable housing solutions.
- Construction Speed: 3D printing takes less time and accelerates the construction process. This automated technology enables faster completion. This speed can be more beneficial in addressing housing deficiencies and disaster relief efforts.
- Sustainability: 3D-printed homes are an engineering practice that reduces waste generation. It uses more sustainable building materials. The precision of the printing process reduces material waste, and some projects incorporate recycled plastics or other sustainable composites. This approach lessens the environmental impact of construction.
- Design Innovation: You will have considerable freedom in your house design. You can easily create more customised and complicated architectural designs (such as curved walls, geographical shapes, etc.). This design freedom, without a hefty price tag, increases the possibilities for architectural innovation.
Challenges & Limitations
Although 3D-printed homes offer countless advantages, there are some limitations that you need to consider:
Building Codes & Regulations
Currently, many existing codes are created only based on conventional construction methods; local, state or national standards have not been designed for 3D-printed buildings. Code compliance requirements can vary from one location to another, and it’s reasonable to expect scrutiny from building and code officials. Regulatory bodies need to adapt to encompass 3D printing technologies to verify the safety and durability of these structures.
Limited Material Options
Currently, 3D-printed homes have limited material options, mainly consisting of concrete-based mixtures, which may not meet all structural or aesthetic requirements.
Limited Roofing Solutions
3D printers mainly focus on building walls. Thus, roofing solutions for 3D-printed homes are somewhat limited. They commonly use traditional roofing methods to complete the structure.
Public Perception
What people think about 3D-printed homes affects how many will accept and buy them. Some may worry about strength, safety, and looks. Introducing people to the benefits and limits of 3D-printed houses and giving clear information can help them trust and accept this new way of building homes.
Concrete Expertise
You need to hire experts in concrete building materials for 3D-printed homes. Concrete dries slowly and reacts to moisture differently than wood. As it dries, it can crack. Normally, builders use joints to control these cracks, but 3D-printed walls may not have joints, so cracks will appear. To protect the walls, they need to be sealed or covered after they are built.
Real-World Examples of 3D-Printed Homes
The following are some examples of 3D printing structures:
3D-Printed House in Chennai
It is India’s very first 3D-printed house, and it is located in Chennai. It was built by IIT Madras alumni in 2021. This single-floor structure, which had an area of 600 square feet, was completed in just five days. The major building material used in this construction is a speciality concrete mix based on ordinary Portland cement.
3D-Printed Villa in Pune
In Pune, Godrej Properties partnered with Tvasta Engineering to launch India’s first 3D-printed G+1 villa. It was constructed in four months; this 2,200-square-foot villa combines innovative design with sustainable construction techniques. The villa outhouse features an energy-saving and nature-inspired design.
House Zero in Austin
Pronounced “House Zero,” the 2,000-plus-square-foot home in East Austin is printed by ICON’s Vulcan construction system and designed by Lake Flato. This three-bedroom, two-and-a-half-bath home incorporates curved walls and biophilic design principles that focus on sustainability and resilience. A proprietary material known as “Lavacrete” was used to print the walls in under two weeks.
Habitat for Humanity’s Virginia Home
The 3D-printed home is located in Williamsburg. It was built in partnership with Habitat for Humanity and Alquist. This has a total area of 1,200 square feet, with a three-bedroom, two-bathroom house. Its exterior walls are printed in just 28 hours.
3D-printed homes can revolutionise the construction industry by reducing the carbon footprint of the environment. This budget-friendly and affordable option can bring India’s poor people close to affordable housing, mainly in areas with increasing housing costs. As technology improves, 3D-printed homes could become a common way to build houses.