A composite material that can be ultimately used in highway construction typically involves the constructing asphalt roads; this material is bituminous concrete. Although concrete roads offer certain advantages, over 90% of roads are built using asphalt, also known as bituminous concrete, due to its superior cost-effectiveness, ability to utilise unskilled labour, and appealing aesthetics. Keep reading to explore bituminous concrete roads, their construction process, and more.
What is Bituminous Concrete?
Bituminous concrete is commonly used for paving parking lots, roads, and highways. A binding agent holds the mixture of stone and other aggregate components together in the final product. Bitumen, a by-product of the petroleum refining process, is the binding material. Like tar, it gets thick and sticky when heated. It also forms a dense surface when cooled. Asphalt is another name for bituminous concrete.
Despite their similar names, bituminous concrete is very different from ordinary concrete and does not contain cement. It stands out due to its distinctive black colour, whereas most cement surfaces are white or grey.
Application of Bituminous Concrete
Bituminous concrete is durable, moisture- and weather-resistant. Furthermore, production and maintenance costs are not excessively expensive. These characteristics have made it a popular choice for a wide range of applications, including:
- Road construction
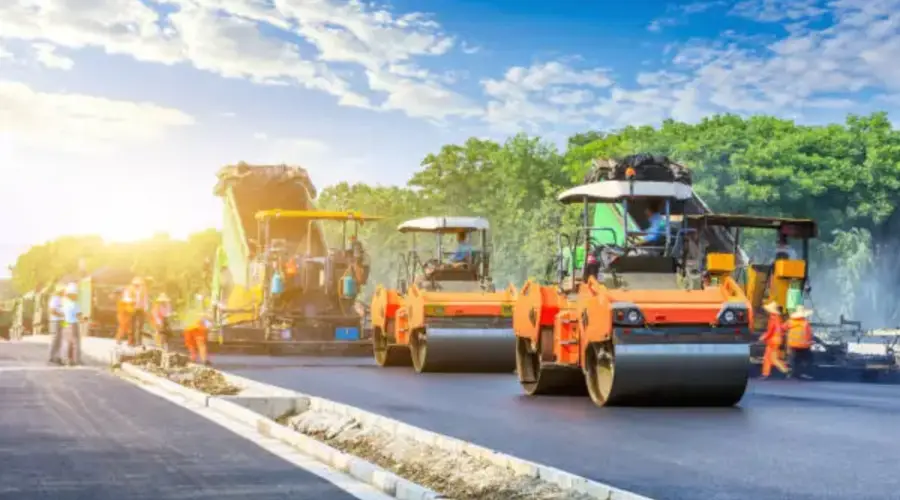
In road construction, bituminous concrete is used to create both the surface layer and the foundational base of roadways.
- Service roads, Driveways and Pavements
Bituminous concrete is often the first choice for sidewalks and driveways. Additionally, it is occasionally used to construct play areas and other surfaces that need to have a durable, non-slip quality.
- Road repair
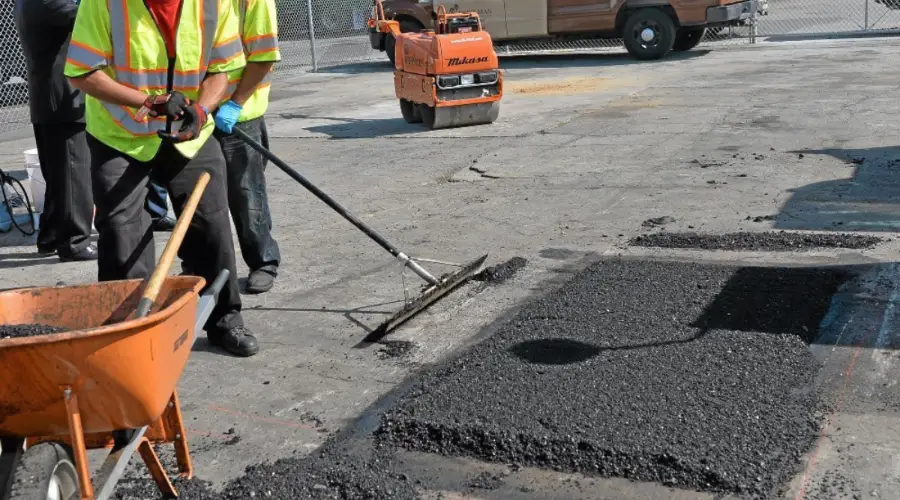
In order to fix or fill in holes and irregularities, bituminous concrete (BC) mix is commonly placed on deteriorated roads. In order to construct new roads and parking lots, it is also placed immediately on top of a base layer of gravel. Large paving machines are used to crush and smooth the surface of the bituminous concrete after it has been poured onto the road.
Benefits of Bituminous Concrete
Airports, parking lots, and other public areas are surfaced with bituminous concrete. Paving equipment is typically used to compact it after it has been laid in layers. It is less expensive, easier to repair, rides more smoothly and quietly, and is more resistant to rutting and cracking than regular concrete. The environmental impact, reduced strength, increased maintenance, and vulnerability to oxidation and weathering are some of its drawbacks.
Composition of Bituminous Concrete
Bituminous concrete has a high level of stability and hardness since it is composed of bitumen, coarse and fine aggregate, and mineral filler. The right bitumen amount and suitable aggregates ensure the desired density.
Bitumen that satisfies IRC & MORTH requirements and is sourced from an authorised source should be viscosity-graded bitumen or bitumen treated with polymers.
Coarse aggregate
Coarse aggregates are composed of crushed rock, crushed gravel (shingles), and crushed air-cooled slag that has been screened through a 2.36 mm screen. They must be devoid of organic matter, dust, soft or friable materials, and other dangerous substances. Aggregates should be cubical, sturdy, and strong.
Fine-grained aggregate
Fine aggregates are made up of crushed stone that has been kept on a 75-micron filter after going through a 2.36 mm sieve. They must be devoid of organic matter, dust, soft or friable materials, and other dangerous substances. They also need to be dry, clean, firm, clear, and strong.
Filler
The filler will be either finely divided cement or hydrated lime, as the engineer determines. It must fulfil the grading requirements specified in MORTH’s table 500-8.
Advantages of Bituminous Concrete
Asphalt paving is still the most widely used material in road building, despite not having the same strength as traditional concrete. The following are some advantages of bituminous concrete roads:
- Sturdy yet simple: They can tolerate years of traffic load and are rather easy to repair or refinish.
- Less noisy and smoother: Compared to cement concrete roads, BC roads provide a quieter and smoother driving experience, which helps to reduce noise pollution around major roads and highways.
- Reduced cost: Bituminous concrete roads are less expensive to maintain initially and over time than cement concrete roads.
- Progressive decay: It refers to BC pavement deformation and failure. Brittle failures are a result of cement concrete pavements.
Although recycled components may not be as durable as new ones, bituminous concrete (BC) roads are also fully recyclable. Some manufacturers incorporate glass aggregate or recycled tires into their recycled asphalt to increase its strength and durability.
Disadvantages of Bituminous Concrete
The environmental impact of bituminous concrete is a key disadvantage in its use. The bituminous binding components in asphalt are derived from fossil fuels, which are naturally finite and non-renewable resources. Furthermore, fossil fuels significantly contribute to environmental contamination through a variety of processes. Toxic chemicals released into the atmosphere during the extraction process contribute to global warming and damage air quality, posing major ecological and public health risks.
Properties of Bituminous Concrete
The key properties of bituminous concrete are as follows:
- Stability: The ability to withstand deformation under repeated or extended stressors with sufficient resilience.
- Durability: The capacity to tolerate deterioration brought on by abrasive forces or weathering. Bituminous concrete withstands harsh weather and traffic wear.
- Flexibility: Bituminous mixtures adjust to the base design and bend without cracking.
- Skidproof: To offer enough protection against sliding off. Helps to stop tyres from skidding by providing enough resistance.
- Impervious: Should reduce seepage of rainwater.
Production and Laying Process
Production of Bituminous Concrete
You have to mix the components of bituminous concrete at the initial stage with crushed stone, gravel, or sand. The mixture comprises 95% aggregate to 5% bitumen.
Additives that consist of fibres, emulsifiers, and polymers may be added to provide greater resistance to water and deformation. The mixture is heated in a batch plant or drum once the ingredients have been combined. The bitumen becomes more fluid and uniformly spread throughout the aggregate as a result of the heat. The mixture solidifies and becomes more cohesive as it cools. In order to produce uniform, high-quality bituminous concrete, this heating stage is essential.
Laying Process of Bituminous Concrete
- Preparing the Base Layer: Fill potholes and imperfections in the base layer with premix chippings for at least a week before adding the surface layer.
- Applying Tack Coat: Apply bitumen at 6.0–7.5 kg per 10 sq.m. for bituminous bases, and 7.5–10 kg per 10 sq.m. for non-bituminous bases.
- Placing Premix: Spread premix from a hot mix plant using a mechanical paver at 121–163°C, ensuring proper layer and camber alignment.
- Rolling: Compact the spread mix with a road roller at a speed below 5 km/h.
- Quality Control: Regularly check aggregate grading, bitumen quality, and the temperatures of mixing and concrete compaction. Test one sample for every 100 tonnes of mix from the hot mix plant.
- Finishing: Use a 3.0 m straight edge to inspect the surface for smoothness, ensuring longitudinal undulations do not exceed 8.0 mm over 300 m and that no more than 10 undulations exceed 6.0 mm.
Conclusion
In road construction and other paving projects, bituminous concrete is a common and long-lasting paving medium. Bituminous concrete can endure for many years with minimal maintenance if the proper production procedure and quality control methods are followed. To guarantee the greatest result, manufacturers must employ the right techniques and materials for laying roads or other paving projects.