Have you ever wondered why giant chimneys emit smoke from brick manufacturing sites? Yes, they are fire kilns and they emit smoke when the bricks are burnt in high temperatures. Burning bricks is one of the important processes in the manufacturing of bricks to instill durable properties.
Burnt clay bricks are commonly used in almost every construction project due to their versatile properties. Here, we take a look at what burnt clay brick is, its manufacturing process, types, properties, applications, and more.
What is Burnt Clay Brick?
Burnt clay brick is a clay brick that is burnt at very high temperatures to add more strength and hardness. These bricks can withstand high temperatures and possess high durability and strength compared to other clay-made bricks.
How Burnt Clay Bricks are Manufactured?
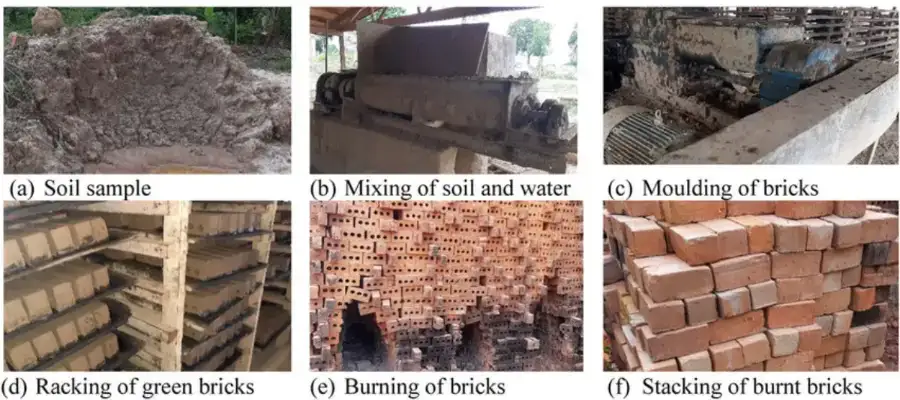
Image Source: Research gate
Preparation of Clay
The process of preparing clay involves six steps such as unsoiling, digging, cleaning, blending, weathering, and tampering.
- Unsoiling: The upper soil surface from which the clay needs to be excavated is removed up to a depth of 200 mm to eliminate impurities and other earthy particles.
- Digging: The clay is then mined manually or using mechanical equipment and heaped above the ground surface.
- Cleaning: The collected clay is cleaned to remove stones, pebbles, and other vegetable matter using a filtering screen.
- Blending: The filtered clay is mixed with sand and straw to improve the quality of the brick.
- Weathering: The blended clay mix is spread out on an open surface for direct exposure to the natural weather conditions for several weeks or even a month to allow plasticity and durable properties.
- Tampering: Adequate water is added to the weathered/seasoned clay, which is then kneaded with the help of labour or cattle two to three times and battered with shovels to make it a homogenous mix, ready for moulding.
Moulding
The prepared clay is transferred to a mould and compressed to eliminate gaps to acquire a good texture and finish, either manually or mechanically using high-powered compressing machines.
Drying
The moulded clay bricks are racked and kept under the sun for drying. Usually, the drying process takes around 3 to 10 days, depending on the climatic conditions.
Burning
After being exposed to the sun, the bricks are burnt in fire chambers (or kilns) at very high temperature (1100°C) for 10 to 40 hours to gain maximum strength and hardness.
Types of Burnt Clay Bricks
First-Class Bricks
The First Class Brick or Class-I brick is burnt at the right temperature and the shapes are perfect. It has a load-bearing capacity of more than 10.5 N/mm² and emits a clear ringing sound when struck. These bricks do not absorb water more than 20% and the efflorescence should be minimal. These bricks are used for load-bearing structures and walls that are exposed to extremely hot temperatures.
Second Class Bricks
The second-class bricks are slightly over-burnt. It has an uneven surface and possesses a slightly distorted rectangular shape. It has a load-bearing capacity of over 7 N/mm² and emits a ringing sound when struck.
They will not absorb water more than 22% of the actual weight. These bricks can be used for load-bearing walls, but cannot be used for exposed walls.
Third Class Bricks
The third-class bricks are either overburnt or underburnt. They have an irregular surface and shape with a load-bearing capacity of over 3.5 N/mm². These bricks produce a dull sound when struck. It is used in non-structural parts of construction, such as gardening walls and landscaping.
Fourth Class Bricks
Fourth-class bricks are kiln-rejected bricks, which are either overburnt or underburnt. The overburnt bricks are dark coloured, hard, and highly irregular in shape. These bricks are used as an aggregate for concrete and as a road metal. The underburnt bricks are yellow with low strength and can be powdered easily.
Properties of Burnt Clay Bricks
Shape & Size
An ideal brick should have a uniform shape and size with sharp edges and perfect parallel sides. They should be of Indian Standard size of 19 x 9 x 9 cm.
Colour
A perfect burnt clay brick should be bright red and uniform in colour.
Texture & Compactness
The burnt fire brick should be of fine, dense, and uniform in texture. The bricks should not possess any cavities, loose grit, unburnt lime, or high efflorescence.
Hardness
An ideal brick should be hard enough to withstand wear and tear. When scratched with hard substances, it should not cause any impressions on the brick’s surface.
Load-bearing test
This test is conducted to determine the load-bearing capacity of the brick. An ideal brick should have high strength (not less than 10 N/mm²). The blocks with higher strength have the capacity to withstand heavy loads.
Water Absorption
The brick is soaked in water for 24 hours and weighed, if the total weight gained is less than 20%, it is suitable for use.
Efflorescence
The brick should not form white patches on the surface when immersed in water or exposed to rain and humid conditions. The bricks with low efflorescence have high durability to withstand wet conditions.
Applications of Burnt Clay Bricks in Construction
- Burnt clay bricks are commonly used for constructing walls, foundations, structural and decorative elements in residential, commercial, and industrial buildings.
- These are mainly made for fireplaces such as chimneys, steel factories, and other high-temperature places.
- They are also used to build cinema halls, theatres, schools, and hospitals, as their density helps in soundproofing and prevents noisy environments.
- The burnt bricks can also be used in retaining walls such as drainage, dams, raised beds, and borders.
Advantages & Disadvantages of Burnt Clay Brick
Advantages of Burnt Clay Bricks
- High strength & Durability
- Weather resistance
- Easily available and affordable
- Absorbs sound
- Natural thermal insulator
- Suitable for almost all types of construction
Disadvantages
- The manufacturing process pollutes the air
- Heavy Weight
- Loss of soil & water
- Waste generation
Conclusion
Burnt clay bricks are known for their strength, durability, and versatility of use in the construction field. These types of bricks are widely used in almost every construction purpose due to their heavy load-bearing, low water absorption, and thermal conductive nature. It is easily available in the market for an affordable price, making it one of the ideal bricks for every type of building.