The usage of refractory castables is surprising. It is a non-metallic material possessing incredible heat resistance and thermal insulation properties. It can be widely used in high-temperature applications to withstand impact. They can often be found in boilers, furnaces, and kilns. From steel to cement and photochemical industries, these castables are the best sellers in the market.
They are composed of granular and powdered materials, moisture, and binders, hence harden without heat. Castables are classified into several types; here we will discuss castables and refractory castables. Understanding their technical aspects can help you choose the best one for your requirements.
What is Refractory Castable?
Refractory castable, also known as acid-resistant castable, has become a popular material in the market. It consists of 13% to 16% sodium silicate solution, 60% to 70% acid-resistant aggregates, and 30% to 40% other raw materials.
The density of refractory castables decides its performance, which includes heavy, medium and lightweight. It ranges from 0.4 to 2.0 g/cm3, widely used in the non-ferrous metallurgy and chemical industry. Its massive quantity of binding agent and moisture content results in high-strength refractory castable.
Types of Refractory Castables
There are various refractory castables available in the market. Here are some of them:
Non-cement Refractory Castables: This type of castable is also recognised as no-cement or cementless castables. It is dried with a special binder before it is exposed to high temperatures. Its lack of CaO content makes it suitable for use in refractory materials, specifically in the alumina industry.
High-Alumina Refractory Castables: High-alumina castables are often used in heat-treatment furnaces, lining tumbling kilns, and other furnace applications like power plants, construction, cement, etc. It is well suited for applications that require exceptional thermal resistance, strength, and high-temperature properties. This type of refractory castable contains an excess amount of alumina content that can range from around 60% to 90%.
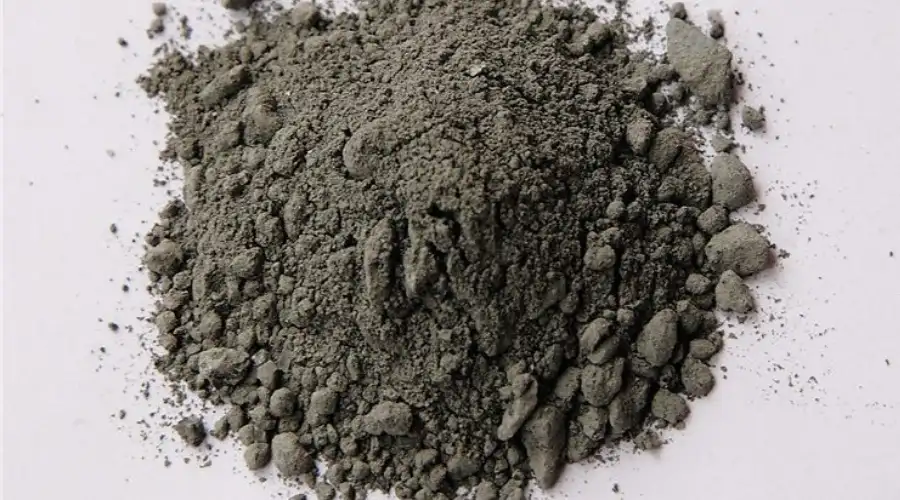
Low-cement Refractory Castables: This is another outstanding refractory castable that offers excellent physical properties like good abrasion, low porosity, etc. Unlike regular dense castable, this type is made of less content of cement and can be used in refractory linings such as cement kilns, blast furnaces, water-cooling pipe binders, and refractory boilers.
Insulating Castables: This is a precise choice to use in cold-face applications, especially in the temperature range from 900 to 1500 degrees Celsius. They are available in various sizes and shapes, containing very low thermal conductivity to reduce the need for fossil fuel and to retain heat.
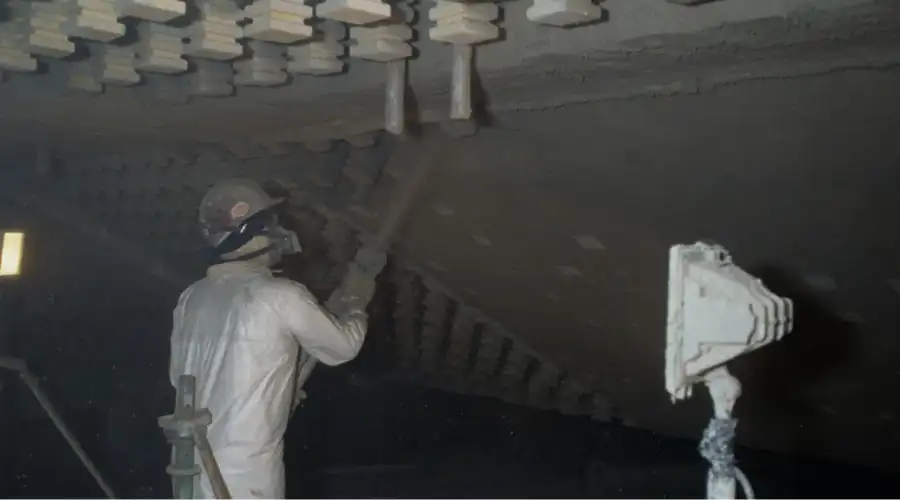
Lightweight Insulating Refractory Castables: This type of refractory castables can also be identified in several sizes and shapes. They are composed of ingredients such as refractory powder, cement binder, and other aggregates/additives.
Ultralow Cement Refractory Castables: It is a kind of castable material that contains a low amount of cement content. They can be suitable for the applications that require excellent performance and durability at high temperatures. It includes calcium oxide between 0.2% and 1% on a calcined basis.
Applications of Castables in Construction
Castable is a versatile material known for its exceptional durability, strength, and fire-resistance. They can be used in several applications, and some of them are:
- Castables are a suitable choice to fill gaps or voids that exist in the concrete slabs and flooring, typically improving their load-bearing capacity and structural integrity.
- They are often used to level the surface and ensure a smooth and perfect finished foundation for subsequent layers.
- They have excellent fire-resistant properties, making them ideal for creating insulated walls and partitions. It reduces heat loss and improves energy efficiency.
- Due to its increased load-bearing capacity, castables are a wise option to reinforce structural elements like columns and beams.
- It can be used in various architectural features like moldings, sculptures, and decorative columns.
Steps for Proper Installation of Castables
Here are the significant steps involved in the installation of castables:
Preparation: It is essential to ensure the substrate is clean, dry, and free from dust. If necessary, you can use a bonding agent to improve the adhesion between the substrate and the castable.
Mixing: You must follow the manufacturer’s instructions when mixing castable with water. An appropriate amount of water is essential to achieve the desired consistency. To hydrate well, leave the mixture for a few minutes, which helps obtain its desired properties.
Applications: You can apply the castable mixture into molds or forms. Now, spread the material evenly and vibrate it to eliminate the voids or air pockets for proper consolidation.
Curing: Castable should be cured properly until the recommended period of time, which may range from 24 to 48 hours. To achieve the desired strength, avoid rapid moisture loss and temperature fluctuations.
Benefits of Using Castables in Construction
Castable is the most essential material in the manufacturing process. But why have they become so popular? Let’s have a look at its significance:
Easy Usage: Castables are simple and effortless to use. Most importantly, they can be molded into different shapes and sizes according to the construction requirement. When prepared with high-quality raw materials, they can efficiently withstand harsh weather conditions without causing any noticeable changes.
Saves Time: One of the biggest industrial advantages is the time saved. It significantly reduces the construction time of the furnaces and promotes productivity. Unlike other materials, they do not require additional baking time.
Strong and Durable: Castables offer exceptional flexural and compressive strength, which prolongs the lifespan of structures. Additionally, they are highly resistant to thermal shock, abrasion, and impacts even in harsh weather environments.
Environmental Benefits: Luckily, castables can be personalized according to the specific needs of the construction. It typically reduces the wastage and material usage. It not only contributes to sustainable construction but also reduces the environmental impacts on structures.
Things to Remember When Using Castables
- It is mandatory to store the castables in a dry, cool area to prevent hardening and moisture absorption.
- Keep them away from extreme temperatures and direct sunlight.
- Avoid using old castables that may be contaminated and affect the overall strength and durability of the castable mix.
- Must use drinking water to mix castable. Being aware of the manufacturer’s instructions can help you achieve the right consistency.
- Mixing castables needs extra care and attention. Too much heat production can speed up the setting time and may fail to achieve the desired strength.
- After pouring the castable, it must set for 24 to 48 hours without causing any disturbance. Cover it with a polythene sheet to avoid rapid moisture loss and maintain proper temperature through the process.
Maintenance and Longevity of Castables
- Monitor and control the operating temperatures to prevent damage and excessive thermal stress.
- Conducting regular inspections allows you to identify the signs of damage, wear, or cracking.
- Limit the exposure of corrosive chemicals, which can degrade the castable material.
- Ensure the castable is properly ventilated to prevent corrosion and moisture buildup.
- Control rapid temperature changes to maintain the originality of castables.
In a Nutshell
Castables are the best-selling material that can withstand high temperatures and harsh conditions. As stated earlier, it is widely used in applications such as furnaces, refractory boilers, kilns, etc. If you are in need, it is recommended to search and find a reliable castable manufacturer in India to have a quality service. Ensure that they have years of experience and offer value-for-money products.