Cellular light concrete (CLC), also referred to as foamed concrete, has been used extensively by builders and homeowners due to its many advantages and easy use. If you are going to build your dream residential or commercial building, choosing the appropriate material is the most important step in initiating a project. CLC is a very smart option for any of your building construction as they are easy to install and reduce the entire weight of the building significantly.
We at Brick & Bolt believe in constructing smarter and more resilient structures that are a testament to time. In this article, we will guide you to know the formation of CLC blocks and other vital aspects in depth.
What is Cellular Lightweight Concrete?
Cellular lightweight concrete (CLC) is a contemporary building material famous for its strength and light weight. It is also known as foamed concrete. It is produced by adjusting the quantities of Portland cement, sand, fly ash, water, and foam. CLC is convenient to handle as it flows easily and does not need compaction like normal concrete.
CLC blocks can be manufactured at the construction site using modern equipment and moulds, which reduces transportation costs. Anyone can easily handle CLC as it is light to carry. It is a popular choice in modern construction and is used widely in residential and commercial buildings.
Composition of Cellular Lightweight Concrete
The three main constituents utilised in the production of CLC are foam, fly ash, and cement.
CLC = Foam + Fly Ash + Cement
- Foam
A foaming agent is applied to produce foam that blends air.. The foam constitutes 40% to 80% of the volume of concrete and contains small bubbles (with a diameter of 0.1 to 1.5 mm).
- Fly Ash
Fly ash is a common industrial waste product that is very challenging to dispose of. Using it in CLC helps reduce waste and makes construction more affordable.
- Cement
Cement binds everything together, forming a lightweight but strong concrete mixture with small air pockets.
Applications of CLC in Construction
CLC blocks are commonly employed in a variety of construction projects due to their lightweight and insulating characteristics.
- They are perfect for acoustic construction, which lowers noise levels in spaces like auditoriums and studios.
- Precast CLC blocks are used for exterior walls because they are strong and long-lasting.
- They help to maintain indoor temperature by providing waterproofing and insulation for roofs.
- CLC blocks support green construction by being eco-friendly.
- They are also used to add extra floors to existing buildings without adding too much weight.
- Common in high-rise buildings, air-conditioned spaces, low-cost housing, and subway construction, CLC blocks offer a cost-effective and sustainable building solution.
- They can also be used for perlite plaster and lightweight perlite concrete.
Physical Properties of CLC
Some physical properties of CLC are as follows:
Drying Shrinkage
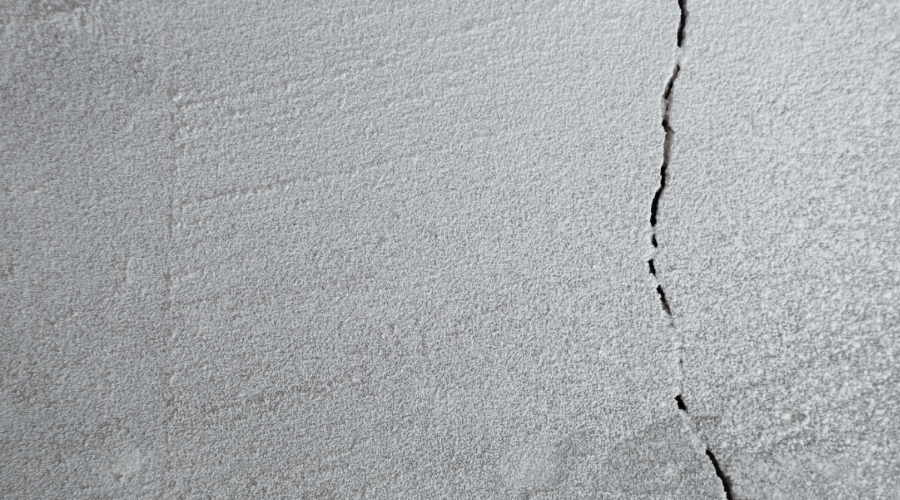
CLC shrinks more than regular concrete because it has no aggregates. Autoclaving can reduce shrinkage by up to 50%. Lower-density CLC shrinks more, while higher-density CLC shrinks less.
Low Density & High Strength
CLC is lightweight, putting less weight on buildings. Denser CLC (1000 kg/m³+) is used in places needing water resistance, like roof slabs and basement filling.
Compressive Strength
When the density of foam concrete decreases, its strength reduces significantly. The cement-sand ratio, water-cement ratio, curing method, sand type and size, and foaming agent all affect its strength.
Flexural & Tensile Strength
CLC has lower tensile strength than normal concrete. Adding polypropylene fibers improves its flexibility and strength.
Benefits of Cellular Lightweight Concrete
The benefits of cellular lightweight concrete are as follows:
- The average density of the CLC blocks ranges from 600 to 800 kg/cum. They are light to handle and easily transported.
- Due to their lightweight nature, CLC blocks help to reduce the overall dead load of a building, which may lead to the optimised use of steel, cement, and other materials, depending on the structural design.
- They do not harm the environment as they are made of fly ash and industrial waste. They are absolutely safe and never release hazardous chemicals into the air, water, or soil.
- They save more energy and power by effectively insulating sound and heat. They are good insulators, which keep your home warm in winter and cool in summer.
- They prevent excessive water absorption with their air bubbles to reduce the chance of wall cracks.
- A 100 mm thick CLC block wall can withstand fire without releasing toxic gases for nearly four hours.
- They are simple to install and use less sand and cement during construction.
Manufacturing Process of CLC Blocks
Three primary processes are involved in the manufacturing of Cellular Lightweight Concrete (CLC): choosing the raw materials, mixing and foaming, and curing under quality control.
Raw Material Selection
Selecting raw materials is a crucial step in all manufacturing processes. You need to select the right materials with the right proportion in order to avoid a defective outcome.
The raw materials used to make CLC are fly ash, water, cement, and a foaming agent. Fly ash, an industrial waste by-product that is hard to dispose of from industries, makes the mix smoother and more affordable.
Cement holds the mixtures together tightly, and water assists in blending the materials and enables them to set and harden. The foaming agent forms small air bubbles, which make the concrete light and easy to handle.
Mixing and Foaming Process
To form a homogenous slurry, fly ash and cement are initially blended with water. A foam generator treats the foaming agent simultaneously, producing stable foam with air bubbles. In order to ensure uniform distribution, this foam is then added to the slurry and well mixed. The end mixture has an even texture and is light.
Curing and Quality Control
The slurry is mixed and then placed into moulds to set. The blocks are either autoclaved for a faster strength development or allowed to water cure naturally for 7–28 days, depending on the curing method. Finally, quality tests are conducted to ensure that the CLC blocks meet construction specifications prior to use by testing density, compressive strength, and water absorption.
Conclusion
In conclusion, cellular lightweight concrete holds its place in modern construction with its lower weight and strength. It can reduce the structural weight of the building and provide long-lasting durability. When compared to other building materials, this CLC is more profitable for builders, architects, and homeowners.
Due to its ultimate strength and good insulation properties, more builders and homeowners are switching to CLC in their homes and other projects. If you want to use CLC blocks in your home, our experts are here to help. Get the best quotation and expert guidance for your project. Call us anytime to discuss your dream home!