When building a structure, prioritising the durability and performance of cement slurry is essential to ensuring the overall strength and longevity of the construction. The right cement slurry mix is essential for achieving optimal bonding, providing resistance to environmental factors, and enhancing the overall stability of the building.
Whether you’re constructing a home, commercial space, or other infrastructure, the correct cement slurry ratio ensures that the structure remains solid and resilient, reducing the likelihood of cracks, water damage, or other long-term issues. In this blog, you’ll discover the ideal cement slurry ratio to support the success of your construction project.
What is a Cement Slurry?
A thin mixture of insoluble substances such as cement, water, and additives that are frequently used in construction to create sturdy, secure foundations, particularly on soft or unstable soil, is called cement slurry. It forms a strong, smooth, and water-resistant coating against the soil when it is poured. It is typically administered by pumping or pouring from a cement truck chute, and its thickness varies according to the project requirements.
For example, cement slurries used in the oil and gas and oil drilling industries usually have a thinner consistency, so they may spread more easily over uneven surfaces. In contrast, residential construction sometimes requires a thicker slurry mixture to provide a strong and water-resistant building foundation.
Importance of Cement Slurry Ratio in Construction
The capacity of cement slurry to produce solid, secure foundations and increase the longevity of structures makes it useful in a variety of significant construction applications. Common applications include:
Soil Stabilisation:
Cement slurry is applied to damp or soft ground to create a firm and secure foundation. The soil is strengthened by this hardened layer, which is also moisture-resistant and appropriate for supporting roads and buildings.
Slurry Walls:
In order to keep structures away from water or unstable soil, cement slurry layers are made. They give structures extra support and stop water seepage.
Paving:
Cement slurry is frequently used to pave driveways and parking spaces. When placed on a prepared base, it creates a smooth, long-lasting, and water-resistant coating.
Road and hole repairs:
Cement slurry is frequently used to fix concrete surfaces like floors and worktops and to fill potholes, fissures, and other damaged areas in highways.
Components of Cement Slurry
The following components are commonly found in cement slurry:
- Cement:
The main binding component, usually Ordinary Portland Cement (OPC), gives the material strength and longevity.
- Water:
Used to make a fluid mixture that makes application easier by hydrating the cement.
- Additives:
Special substances used to change specific characteristics, such as
- Retarders: Reduce the setting time.
- Accelerators: Quicken the time it takes to set.
- Plasticisers: Increase fluidity without the need for more water.
- Weighting agents: Modify density according to particular uses.
- Fillers:
In certain applications, materials like sand or fine aggregates are used to control consistency or lower costs.
- Chemical Admixtures:
Improve certain qualities, such as resilience to extreme weather or durability. The intended application and environmental factors are taken into consideration when adjusting these components.
How to Calculate Cement Slurry Ratio
Follow these steps to calculate the cement slurry ratio for your construction project:
1. Understand the Cement Slurry Ratio
The slurry ratio is often defined as the ratio of water to cement (W: C) by weight or the volume ratio of components. For the majority of applications, a typical water-to-cement weight ratio falls between 0.4 and 0.6.
2. Determine the Inputs you Require
Cement Weight (C): Typically expressed in pounds or kilograms.
Water Weight (W): Typically expressed in pounds, kilograms, or litres (1 litre of water is equivalent to 1 kg).
3. Calculate the Ratio
Weight Ratio (W: C) = Total Weight of Water ÷ Total Weight of Cement.
Volume Ratio (if aggregates or additives are included): Adjust proportions by volume using component-specific densities.
For instance:
50 kg is the weight of cement.
25 kg is the weight of water.
The ratio of water to cement is equal to 25 ÷ 50 = 0.5.
4. Modify the Ratio for Specific Requirements
Adjust the ratio to account for:
- Workability: For a thinner slurry, add more water; for a thicker mixture, add less. Increasing water quantity increases workability, but reduces strength and vice-versa.
- Strength: For greater strength, reduce the water-to-cement ratio.
Keep in mind that too much water weakens the cement paste. Before mixing on a large scale, always test tiny quantities.
Factors Affecting the Cement Slurry Ratio
Several factors that affect the strength of the cement slurry ratio are as follows:
Material Quality
Using high-quality cement and clean, fresh water guarantees adequate hydration, which influences the strength and bonding of the slurry. The water-to-cement ratio must be carefully regulated to obtain the desired consistency. Too much water weakens the mix, while too little makes it difficult to work with. Additionally, additives such as accelerators or retarders may be used to vary setting time and workability depending on specific project requirements.
Environmental and Site Conditions
The performance of cement slurry is also influenced by environmental factors such as temperature and season. High temperatures can reduce the setting time, whilst cold temperatures slow it down, necessitating changes to the mix. The type of foundation soil conditions also play a role, since some soils may require a thicker slurry to maintain stability. Proper mixing and positioning are critical for maintaining consistency and preventing structural weaknesses.
Testing and Equipment Maintenance
Finally, testing and quality control are critical for getting the intended outcomes. Before applying the slurry on a broad scale, small-scale tests should be performed to confirm that it has the necessary strength and consistency. Proper equipment maintenance and adherence to established mixing standards are also essential for optimal slurry performance, which contributes to the long-term stability of residential construction.
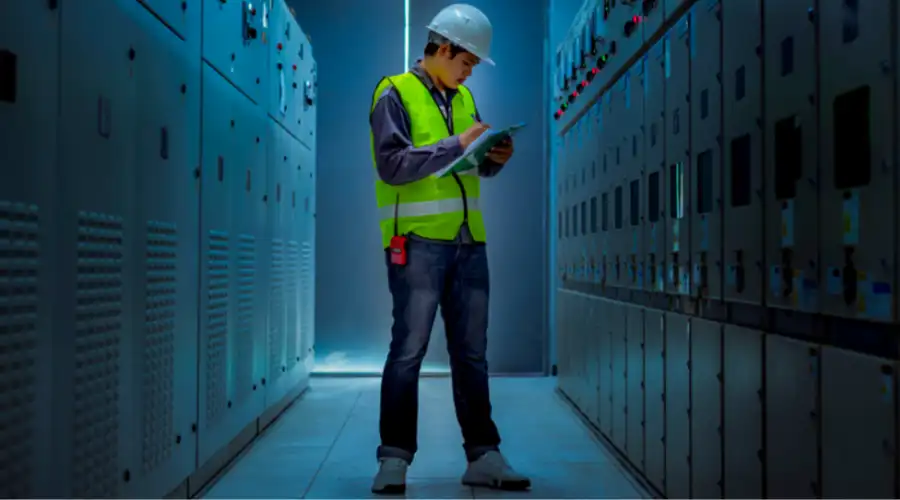
Steps to Mix Cement Slurry Correctly
You’ll need certain materials and tools to make a cement slurry.
Ingredients:
Depending on the purpose, cement, water, and optional chemical compounds.
Tools:
- container for mixing
- Tools for mixing (such as a drill mixer, mixing paddle, or comparable instruments)
Procedure for Making Cement Slurry:
- Measure the cement.
- Based on the needs of your project, calculate how much cement is needed, then put it in the mixing container.
Gradually Add Water:
While mixing, gradually add a small amount of water to the cement. To reach the correct consistency, keep adding water little by little. The water-to-cement ratio depends on the type of cement and how it is used. Using your mixing tool or a cement mixer, blend well.
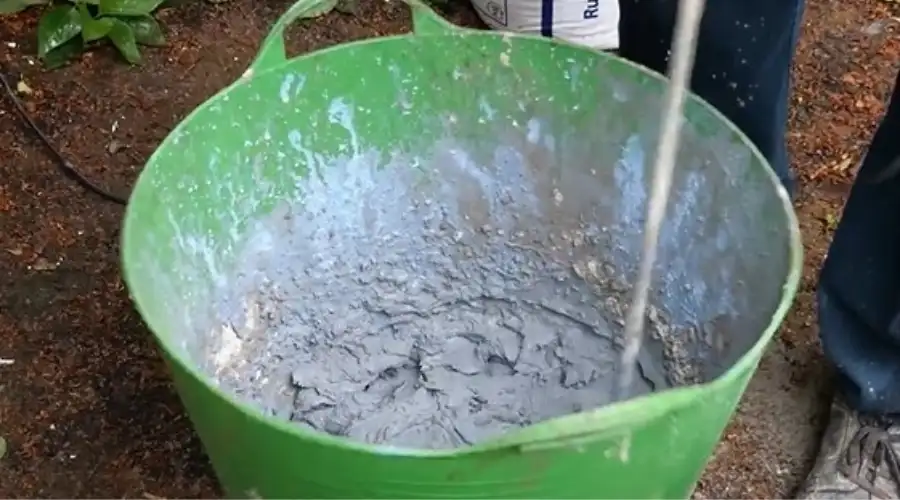
Additives (Optional):
If necessary, gently include additives into the mixture while mixing. Make certain that the slurry is fluid, consistent and without lumps.
Verify the Consistency:
Check the workability and flow of the slurry. Make any necessary adjustments to the cement or water to achieve the proper consistency for your specific usage.
Conclusion
Cement, water, and additives are mixed in the right proportion to produce an exact outcome of cement slurry. It is used to bind stones, tiles, or bricks in a building. It creates a strong, durable glue between surfaces that supports structures and keeps moisture out. When applied properly, cement slurry can increase a surface’s resistance to water. When applied as a coating or in regions where water seepage is common, it creates a strong connection and serves as a barrier to stop moisture entry. Due to the flexibility it offers, cement slurry can be applied both indoors for applications like tiling and fracture treatment and outdoors for long-lasting constructions like pavements and bridges.