Bricks are small rectangular blocks that have been primarily used in the construction industry for a long time. They are uniform in size, shape, and colour, which, when properly arranged, gives strength, uniformity, durability to the structure. They have a wide range of applications in the construction. So, what makes brick a more reliable construction material? In this blog, we take a detailed look at the components of bricks.
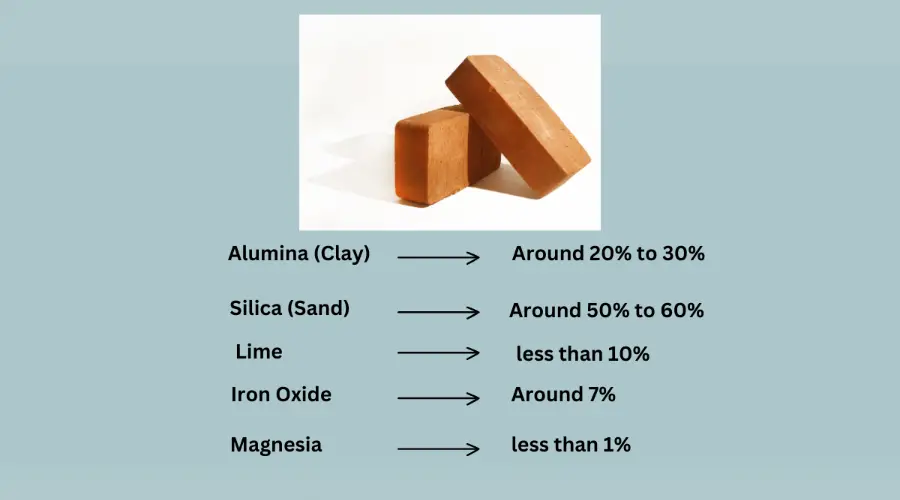
Primary Components of Bricks
Alumina (Clay)
Alumina is the primary raw material for all clay bricks. Around 20% to 30% of the brick contains alumina. It is an essential component that imparts clay plasticity and helps mould the bricks into suitable shapes. However, excess alumina could lead to shrinkage, cracking and warping during the drying & firing process. High alumina in clay can be treated by adding sand and reduce the risk of cracks.
Silica (Sand)
Silica or sand in clay bricks appears as free sand or as silicate of alumina. Around 50% to 60% of the brick contains silica. It plays a major role in maintaining the shape and gives resistance to the brick against cracks, shrinkage, and warping. It also improves the hardness, heat resistance, and durability of the bricks.
However, excess silica content in brick reduces the cohesiveness between the raw materials and makes the brick brittle. In some cases, the uncombined silica can be beneficial by reducing the shrinkage and heat resistance of clays with low alumina content.
Water
Water is another primary source of raw materials that helps mix the other primary materials into workable consistency and shape the bricks. Although being a primary raw material, the water is dried out to achieve the maximum strength of the brick. An excess of water increases manufacturing time, and a poor drying process results in low-quality bricks.
Secondary Components of Bricks
Lime
Lime is added to the raw materials to help silica melt during the firing process and bind the particles together to improve cohesion. Typically, less than 10% of the brick contains powdered lime. It is always added in the powdered state, as lump lime could turn into quick lime during firing, resulting in expansion and splitting when exposed to moisture. An excess of lime leads to over-melting and makes the brick lose shape.
Iron Oxide
Around 7% of the brick contains iron oxide, which provides flux in brick earth and helps melt and bind the particles. It also gives the bricks a red colour during firing under ample oxygen. It improves the brick’s strength, hardness and impermeability and lowers the clay’s melting point.
Magnesia
Magnesia is added in small quantities, typically less than 1%. This imparts a yellow tint to the bricks, reducing the shrinkage during drying. It helps soften the clay and minimises warping during the firing process. However, excess magnesia can result in the decaying of bricks over time.
How Components Affect Brick Properties?
Lime
An excess of lime changes the brick’s colour from red to yellow. When lime is added as a lump, it absorbs moisture, which causes expansion and leads to cracks and disintegration.
Alkalis
Alkalis in soda or potash are a flux during the burning process and cause the bricks to fuse, twist, and warp. It absorbs moisture from the atmosphere, leading to dampness and efflorescence in the bricks.
Pebbles, Stones & gravels
If the clay or sand contains coarse particles such as pebbles, stones and gravel, it leads to poor mixing and reduced strength and uniformity in bricks. Pebbles and gravel could cause cracks in bricks during handling or construction, which leads to poor structural integrity and appearance.
Iron Pyrites
Iron Pyrites in bricks can oxidise and decompose the bricks under high temperatures, leading to splits and disintegration. This may lead to bricks losing their colour and uniform appearance.
Organic Matter
Any organic matter in the brick will burn during firing, leading to the formation of voids. This could make the brick porous and lose its overall strength.
Bricks Production
Preparation of Clay
- Unsoiling: The upper surface of the soil where the clay needs to be mined should be removed up to a depth of 200 mm to eliminate impurities and other earthy particles.
- Digging: The clay is excavated manually or using mechanical equipment and heaped above the ground surface.
- Cleaning: The excavated clay is screened to remove stones, pebbles, and other vegetable matter using a filtering screen.
- Blending: The filtered clay is mixed with sand and straw in an adequate quantity and blended into a mix by adding a small amount of water to improve the quality of the brick.
- Weathering: The blended clay mix is stretched on an open surface for direct exposure to natural weather conditions for several weeks or even months to improve the plasticity and durable properties.
- Tampering: Adequate water is added to the weathered/seasoned clay, which is then kneaded twice or thrice with the help of labour or cattle and battered with shovels to bring the clay to a homogenous mix suitable for moulding.
Moulding
The prepared clay is poured into a mould and compressed to remove the air voids and gaps to achieve a good texture and finish. The moulding and compacting can be done manually or mechanically using high-powered compressing machines.
Drying
The moulded clay bricks are racked and kept under the sun for drying. This process usually takes 3 to 10 days, depending on the climatic conditions.
Burning
After exposure to the sun, the bricks are burned and moved to the fire kilns, where they burned at a very high temperature of up to 1100°C for 10 to 40 hours to attain maximum strength, durability, and hardness.
Conclusion
Bricks are an essential construction material, and understanding the right brick components and manufacturing process is crucial. This blog aims to enhance your knowledge of the primary and secondary components, how an excess can harm the bricks, and the manufacturing process itself.
FAQs
Sand is used in manufacturing bricks to maintain their shape and resist the brick against cracks, shrinks, and warps. It also improves the hardness, heat resistance and durability of the bricks.
Lime is used to help silica melt during the firing process and bind the particles together to improve cohesion with other raw materials.
Additives such as wheat husk, fly ash, Iron Oxide, Calcium Oxide, Potassium Oxide, and Magnesium Oxide are used along with the primary and secondary components to improve the strength of the bricks based on the needs and requirements.