Concrete mix design is a meticulous engineering process. It determines the accurate proportion of cement, water, fine aggregates, coarse aggregates, and chemical admixtures to create concrete with desired properties.
Each of these raw materials possesses unique physical characteristics. By carefully considering these significant factors, engineers can achieve the structures with enhanced strength, durability and workability. Depending on the construction needs, professionals decide the concrete mix ratio with the intent of improving strength and durability. For instance: bridges, flatwork, walls, and underground pipes – the construction of every project needs concrete with different properties.
The process also involves selecting the suitable ingredients and appropriate quantities of concrete mix, which significantly impacts the final product. This article provides a complete guide to concrete mix design and its methods.
What is Concrete Mix Design?
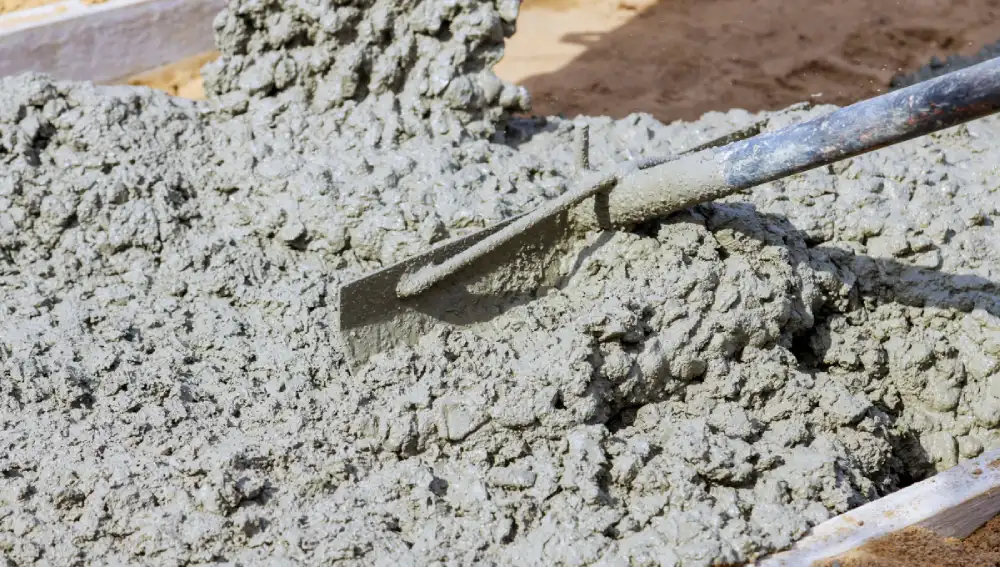
Concrete mix design is a critical process to define the type of ingredients, and the proportions to use them, in order to create concrete with expected technical specifications, enhancing the structure’s strength with desired properties. These properties include workability, durability, strength, and cost-efficiency. It can vary depending on the project needs.
Methods of Concrete Mix Design
The important methods used in the concrete proportioning are as follows:
Maximum Density Method
This method involves weighing the concrete aggregates, using the proportion with heaviest weight for the same volume. It is a unique approach with the principle of obtaining dense and workable concrete. The process particularly requires a box filled with numerous amounts of fine and coarse particles. During this method, the proportion that produces the heaviest weight is used.
It is estimated using the following equation:
P= 100 x (d/D) x 0.5
Here, P denotes % by weight of matter finer than diameter (d).
D represents the maximum size of aggregates.
Arbitrary Method
In this approach, the proportion of cement, water, sand and related aggregates is randomly chosen, while checking for minimal air voids. However, to achieve the desired workability the amount of water in the cement paste is adjusted as required.
For normal construction work, the preferred mix ratio will be 1:1.5:3 and 1:2:4, while for the foundations and mass concrete work, the ratio may be 1:4:8. If the construction subsequently requires higher strength and grade, concrete with a ratio of 1:1:2 is used.
Fineness Modulus Method
The fineness modulus method describes the proportion of coarse and fine aggregates in a concrete mix. It is based on the particle size distribution and is usually represented in index numbers.
The sizes of aggregates play a crucial role in achieving the determined durability, workability, and strength of concrete. The fine aggregates typically generate a Fineness modulus ranging from 2.3 to 3.1 while the value for coarse aggregates is 5.5 to 8.0.
Surface Area Method
The surface area method is a sophisticated approach that minimizes the total surface area of aggregates, reducing the cement paste needed in the mix. When optimizing the amount of cement paste requirements, the concrete mix can be stronger, denser and more cost-effective.
Benefits of Proper Concrete Mix
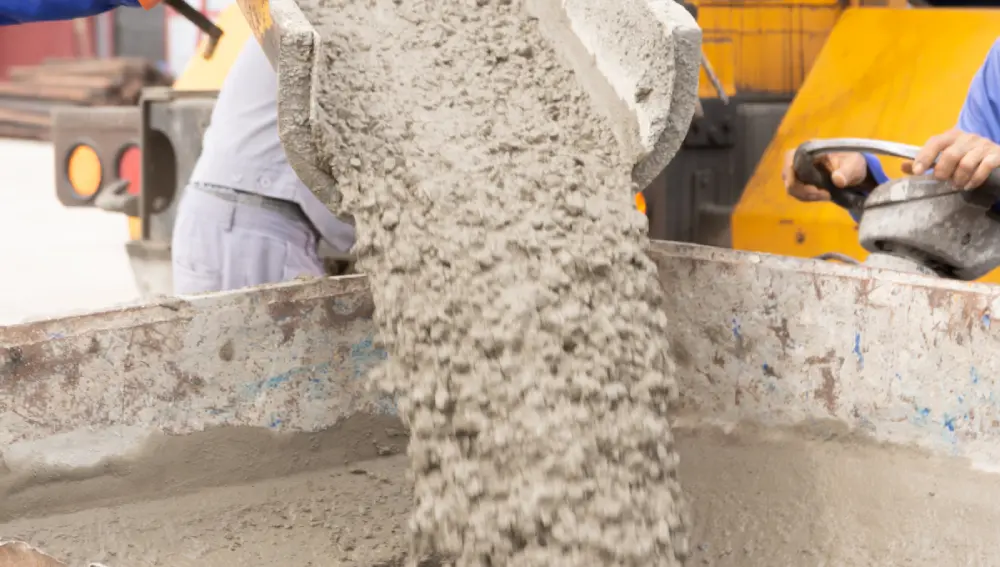
The proportions of ingredients and other components like admixtures potentially impact the final concrete product. The proper concrete mix ensures:
- Strength: Concrete with proper mixing can withstand the intended loads without causing any shrinkage or cracking.
- Durability: A right mix ensures the longer lifespan of the structure withand resistance to weathering, chemical attack and cracking.
- Cost-effectiveness: Estimating the required level of ingredients avoids waste and optimizes costs.
Types of Concrete Mix Design
The following are the types of concrete mix designs.
Design Mix Concrete
The primary purpose of a designed mix is giving concrete the essential strength. Not only the strength, you can obtain all the desired characteristics through both the fresh and hardened stages of concrete. The properties of fresh concrete can be optimized to achieve the required workability and performance of concrete.
During the making process, there are various standard guidelines needed to follow including the IS method, BS method and ACI method. Before applying for the work, this method is tested in different applications to ensure its final results.
Nominal Mix Concrete
The nominal mix concrete contains lower strength when compared to the design mix. Hence it is preferred for simpler, unimportant and small-scale concrete projects. The fixed ratio of ingredients like cement, aggregates, concrete, and sand is used to achieve a certain strength.
According to the ‘Indian Standard – IS 456:2000’, this type is used for concrete of M20 and lower grades such as M5, M7.5, M10, M15.
For example: M indicates mix design and 20 is standard strength of concrete. The mixed ratio of M20 is fixed at 1:1.5:3. It means 1 part of cement, 1.5 parts of fine aggregate, and 3 parts of coarse aggregates.
S.no | Concrete Grades | Concrete Mix Design Ratio(Cement: Sand: Coarse Aggregate) |
1 | M5 | 1:5:10 |
2 | M7.5 | 1:4:8 |
3 | M10 | 1:3:6 |
4 | M15 | 1:2:4 |
5 | M20 | 1:1.5:3 |
6 | M25 | 1:1:2 |
Factors Affected by Concrete Mix Design
Here are the primary factors affected by concrete mix design:
Workability of Concrete
Insufficient workability causes incomplete compaction that severely influences strength, surface finish and durability of concrete. Additionally, high workability concrete is mandatory for narrow and complicated sections containing various corners and inaccessible parts. It ensures achieving full compaction at a reasonable effort.
Durability of Concrete
Durability determines the ability of concrete to withstand harmful environment conditions. In general, high strength concrete is more durable than low strength concrete. Using the right concrete mix proportions ensures that the concrete can resist environmental forces and chemical attacks, while reducing porosity and ensuring longevity
Quality Control
Concrete strength varies during every batch of pouring. The variability in the concrete strength is inevitable during production. Controlling these differences is paramount to maintain the structure quality throughout the project. These variations can be identified and adjusted by using a uniform concrete mix design.
Summary
A well-designed concrete mix ensures the success of any structural project. It ensures provision of strong, cost-effective and durable concrete, resisting shrinkages. Choosing qualified professionals can ensure the selection of the right kind of concrete mix design. They are proficient in basic principles, and can implement suitable methods to meet the requirements of the desired structure.
FAQs
The best concrete mix significantly includes Portland cement, aggregates and water. For achieving higher strength, a low water-to-cement ratio is preferred with the inclusion of admixtures like plasticizers. The mix design can be tailored according to the environmental conditions and specific requirements of a project.
Due to the presence of harmful salts and contaminants, sea water is not advised for mixing concrete. Meanwhile, if it is used in reinforced cement concrete, it leads to the corrosion of steel reinforcements and weakens the concrete structure.
A nominal mix is a suitable method for small-scale structures, free from any complexities where the precise strength is not essential. The design mix can be used in high-strength applications or critical structures in which workability is a primary characteristic.