Different types of plastic are quickly becoming integral materials used in the construction industry. These plastic types are often cost-effective and lightweight, changing the way building structures can be constructed and/or strengthened. One such material is Fibre Reinforced Plastic (FRP), which offers several benefits over conventional building materials like steel, aluminium and glass. Read on to learn all about what FRP is, its types, FRP products and their applications in construction and the pros and cons of FRP material.
What is FRP?
Fiber Reinforced Plastic is a type of composite polymer made of polymer matrices and fiber. Regular plastic consists of only a matrix, while fibers/ filaments are introduced in FRP to reinforce this matrix, transforming plastic from a relatively weak material to a stiff and strong construction element. Fibers can be introduced in the polymer in different two-dimensional or three-dimensional patterns,—such as stitching, knitting, weaving and braiding—depending on the material strength required. Thus, FRP can be manufactured in various forms, types and designs, enabling diverse applications in construction.
Advantages of Using FRP in Construction
Significant benefits of using FRP in construction are:
- Strength to Weight Ratio: FRP has a very high strength to weight ratio, meaning that lightweight FRP components can substitute much heavier elements with the same size and strength.
- Corrosion Resistance: Unlike wood (which rots) and metal (which rusts), FRP is not vulnerable to normal weather conditions. With minimal maintenance, the material can last for decades without getting degraded, depicting its immense durability.
- Thermal and Electrical Insulation: FRP composite has very low electrical and thermal conductivities, allowing its usage in components requiring high thermal and electrical insulation.
- Recyclability: Once in disuse, composite fiber reinforced plastic can be recycled by melting and remoulding it into the desired shape and form. Although it is not a very eco-friendly material, its recyclability encourages sustainable building practices.
Types of Fibre Reinforced Plastic
FRP has two major components- the polymer (FRP resin or matrix) and the fibers. Based on the materials used for forming each of these components, the FRP material can be classified into numerous types:
Carbon Fibre Reinforced Plastic
Carbon Fibre Reinforced Plastic (CFRP) consists of Carbon fibers in polyester, nylon or vinyl ester polymers. Carbon atoms are bonded to form crystals that are aligned parallel to the longer axis of the fiber, giving the material high stiffness, tensile strength and temperature tolerance. CFRP is extensively used for strengthening existing RCC structures like beams, columns and bridges.
Glass Fibre Reinforced Polymer
Glass Fibre Reinforced Plastic (GFRP/GRP) or fibreglass reinforced plastic consists of thermosetting or thermoplastic resins with fine glass fibers. Since this type has a lower density, it is not as strong or rigid as Carbon FRP. However, GFRP is much cheaper and less brittle and is used for making railway sleepers and for reinforcing concrete structures.
Apart from these two common types, a few other materials that can be used for reinforcement in FRP are wood, asbestos, paper, basalt and aramid, while epoxy and phenol formaldehyde are other resin materials.
How is FRP Used in Construction?
FRP commonly has the following applications in the construction industry:
FRP Structural Elements
Structural elements like beams, columns and rafters in buildings can be made of Fibre Reinforced Plastic. Box sections, I-sections and wide flanged sections are some of the common types that can be used for creating the framework of bridges, multistorey buildings, railway platforms and marine structures. Such structures are much lighter than conventional RCC structures, although their strength must be carefully calibrated.
FRP as Concrete Reinforcement
FRP bars, prestressing tendons and grids can be used in reinforced concrete structures as a substitute for steel rebars. In contrast to steel, FRP bars do not rust or get corroded, making them highly durable. They are also much lighter in weight than steel rebars, significantly reducing the structural weight of buildings.
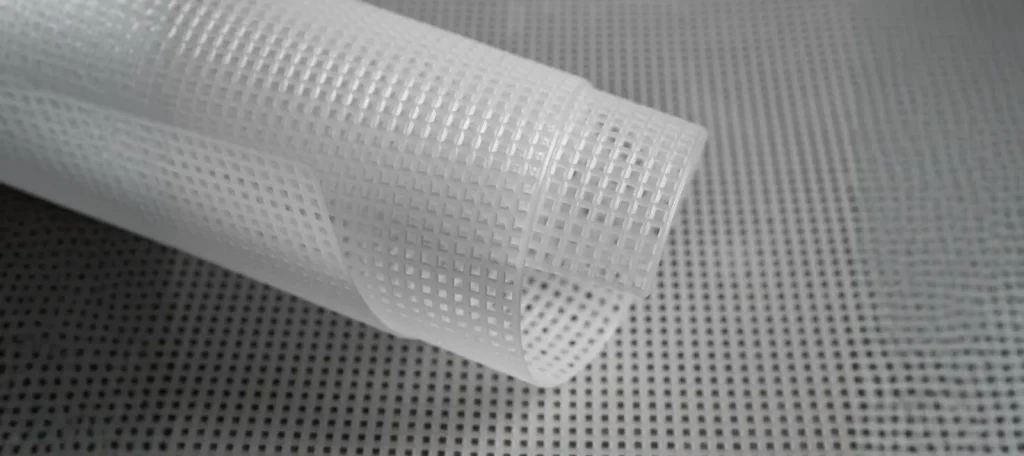
FRP Building Elements
Building components such as doors, windows, roofing sheets and cladding panels can be made with FRP. Here, their non-corrosive, lightweight and cost-effective nature are especially beneficial. Other construction elements like utility poles, drainage systems, pipelines and railings can also be made with FRP, depicting the material’s versatility in the field.
FRP in Retrofits and Repairs
Due to their strength and flexibility, FRP sheets, panels and strips can be used to create jackets around existing structural RCC elements like beams and columns whose concrete is corroding. They can also be used to strengthen steel, wood and masonry structures by increasing their load bearing capacity, forming a crucial part of retrofit and repair processes.
FRP Products in Construction
Some of the commonly used FRP products in the construction industry are:
- Fiber Reinforced Plastic Sheet/ FRP Panels: FRP sheets and panels are commonly used for roofing due to their flexible, lightweight and weatherproof nature. Such sheets are available in various profiles—like plain, corrugated and rectangular—in thicknesses ranging from 0.5mm to 15mm.
- FRP Pipe: An FRP pipe is waterproof and airtight, making it ideal to be used for the conveyance of water, petrol, chemicals, sewage, oil, gas and air (in HVAC systems).
- FRP Grating: Gratings with I or T shaped FRP bars can be made for usage on floors or pavements with heavy foot traffic, offering high strength and durability.
- FRP Doors: The light weight, durability and cost effectiveness of FRP doors makes them a popular choice in residential, industrial and commercial buildings.
- FRP Staircase Components: Staircase landings, treads and railings can be made with FRP. These components require low-maintenance as they do not rust or rot and can also be customised to produce versatile aesthetics.
Limitations of the FRP Material
Fiber Reinforced Plastic presents the following challenges that limit its usage in the construction industry:
- Fire Resistance: Most types of FRP (except Carbon FRP) are combustible, thus posing risks to fire safety in buildings. Although fire resistant materials can be integrated with FRP to make it fireproof, this can be expensive.
- Temperature Resistance: FRP cannot be used for long durations in regions with very hot climatic conditions. Constant exposure to temperatures above 50 degree celsius can lead to a loss in strength and deformation of the material.
- Weathering: UV radiations, very strong winds and harsh chemicals can have a negative impact, with scratches and discolourations in the FRP coating being common issues. It is also difficult to recoat or repaint the material.
Using Reinforced Plastic in Your Project
Despite the few drawbacks, Fibre Reinforced Plastic offers numerous advantages over conventional building materials, enabling its extensive usage in the construction industry. It serves as a suitable alternative to steel and RCC in multiple scenarios, leading to its growing popularity across the world. Brick & Bolt, a tech-enabled company, aims to use the latest materials and technology in all of its building projects. For procuring premium end-to-end construction services guaranteed with thorough analysis of new materials like FRP, contact Brick & Bolt today!