Steel is the backbone of any structure; it holds up a building and makes it stand for itself for ages. Although they give unmatched strength and versatility, they have the maximum chance of rusting and corrosion, which will lead to a shorter life expectancy for the building.
When you search for something that a person can insure for durability, then galvanised steel will be considered for selection. It is not a standard steel as these steels are designed to have a balance between strength, long life, and its corrosion-resistant.
What is Galvanised Steel?
Galvanized steel is coated with zinc to improve its corrosion resistance. The coating protects the substrate against moisture—or temperature-induced damage. The steel is dipped into molten zinc, which subsequently bonds to it as part of its chemical structure.
Galvanisation Process of Steel
The galvanisation process of steel is pretty straightforward, and here is the step-by-step process.
- The steel is first cleaned using degreasing to remove rust and other impurity deposits.
- After cleaning, the steel undergoes a pickling process, where the steel is submerged into diluted hot sulphuric acid.
- This steel then goes through the fluxing process, where the surfaces are prepared by applying a layer of saline coating, which helps provide the necessary binding between the iron and steel. The fluxing process is done in an aqueous solution, particularly zinc-ammonium chloride.
- After fluxing, the steel is galvanised by dipping it into a bath of molten zinc at a high temperature of approximately 450 degrees Celsius. This helps to bind the zinc to the steel, and the galvanised steel attains the properties of the two metals.
- Another form of galvanisation is through spraying zinc onto the steel, however, it may not be that effective in blending with the steel, forming a weaker layer of zinc.
- After galvanisation, the seal is inspected for consistently coated throughout the steel.
Benefits of Galvanised Steel
- The initial cost of galvanized steel is lower than that of most treated steel. Secondly, it is ready to construct, as it does not require additional surface preparation, inspections, painting/coatings, etc. This helps companies save on additional expenditures.
- Galvanisation typically renders an industrial steel to last more than 50 years on average, but even when the steel is subjected to extensive moisture, it can serve for more than two decades. No maintenance is needed. Moreover, the greater durability in the finish of the steel product increases the reliability of the product itself.
- The anode ensures that the exterior surfaces of any damaged steel are protected beneath the zinc coating. The steel section does not need to be completely in contact, as the zinc will still corrode first. This, in turn, causes the coating to preferentially corrode to the steel, thus providing sacrificial protection to affected areas.
- Iron in steel is susceptible to rusting, but zinc creates a barrier so that moisture or oxygen cannot reach the steel. Galvanized steel protects well, even sharp corners and recesses unprotected by other coatings. Such areas are then highly resistant to damage.
Application of Galvanised Steel
- Building Frames
- Duct Work
- Fences
- Ladders
- Staircases
- Support Beams
- Nails, Nuts, and Bolts
- Computer Castings
- Precision Instruments
What is Galvanised Steel Sheet?
Galvanised steel sheets are zinc-coated steel sheets that provide enhanced corrosion resistance for a wide range of applications. It is prepared in the same way as the galvanised steel is produced, by dipping the steel into molten zinc at 450-degree Celsius. They are highly used in various construction, automotive, electrical and agricultural applications.
Uses of Galvanised Steel Sheet
- Roofing Systems
- Wall Cladding
- Structural Components
- Vehicle body panels and chassis
- Building Electrical Goods
- Agricultural Silos and Storage Bins
- Machinery Covers
- HVAC Ductwork
- Forming Tables, Chairs and Shelving Units
Galvanised Sheet vs Stainless Steel
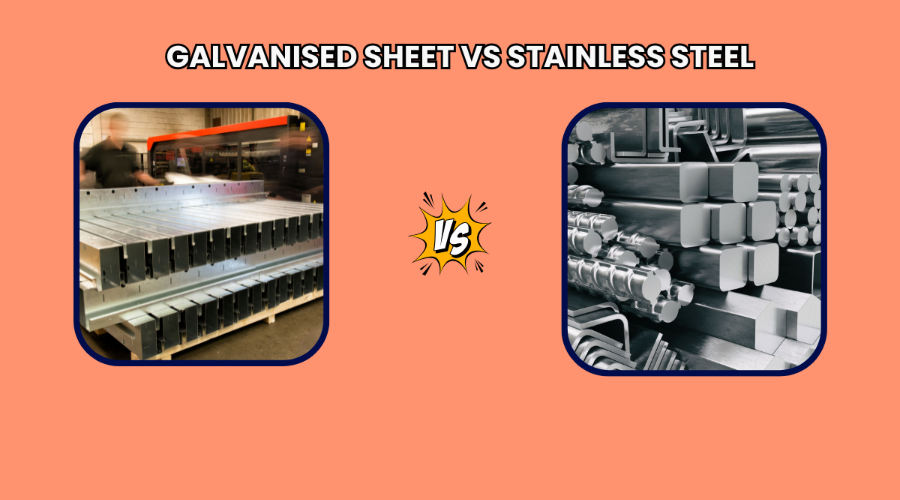
Feature | Galvanised Sheet | Stainless Steel |
Material Composition | Steel coated with a zinc layer. | Alloy of iron and at least 10.5% chromium |
Corrosion Resistance | Provides moderate resistance against corrosion, as zinc coating can wear off over time. | Excellent resistance to rust and corrosion |
Durability | Less durable, as they can corrode when the zinc coating is damaged. | Highly durable and can last longer, even in harsh conditions. |
Strength | Offers moderate strength, and is comparatively weaker than stainless steel. | Offers high strength, suitable for structural applications |
Weight | Lighter compared to stainless steel. | Heavier than galvanized steel. |
Maintenance | Requires frequent maintenance, especially to prevent deterioration of zinc coating. | Requires low maintenance, and resists staining and rusting over time. |
Cost | Compared to stainless steel, they are inexpensive. | They are more expensive due to the alloy content and durability. |
Appearance | They are of a matte, and slightly dull finish. | They have a shiny, and reflective surface that improves over time. |
Applications | RoofingFencingAusomative | High-end kitchenwareMedical equipmentArchitecture |
Conclusion
To sum it up, galvanised steel can be a great alternative to regular steel that is used in construction. They prove to be the more durable and corrosion-resistant material for construction at an economical cost. The protective coating of zinc to iron or steel prevents rust and ensures that the coating covers those places, such as roofing and structures, which use galvanised material. Galvanised steel is as tough as it is sustainable, all to meet modern construction demands with reliability.