It doesn’t matter if you are engaged in building a home or a high-rise building; the quality of cement is the primary concern. But don’t be under the impression that all the qualities of cement remain the same. Some give the desired results, and some can be inferior.
This is the reason builders are advised to evaluate the cement quality before purchasing. Cement is a fundamental building material acting as a binding agent for both mortar and concrete. If the quality of the cement is up to standard, you can enjoy stronger construction with fewer repairs and maintenance.
To understand the differences and variations between good and bad quality cement, read this article. It uncovers certain significant factors to ensure the quality of cement before buying.
Overview on Cement Composition
Cement is primarily composed of materials like iron ore, limestone, sand, and bauxite. They are commonly found in a grey coloured powdery form packed within sturdy paper bags. Additional raw materials, like slate, chalk, and clay, are also part of the composition. During preparation, these ingredients are processed and subjected to heat at approximately 1500 degrees Celsius. This process results in a fine grey powder, which is packed and sold in the market.
Importance of Checking Cement Quality
Checking cement quality ensures the structural integrity and durability of the construction. When the cement possesses all essential properties, it improves the overall strength and quality of the structure. Consequently, you don’t need to spend additional costs for repair and maintenance.
How to Check Cement Quality with Laboratory Testing?
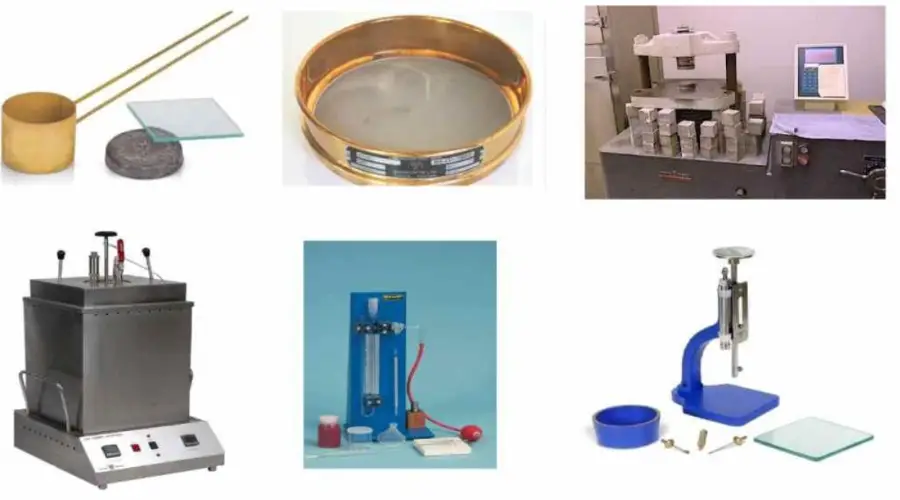
The quality of cement is verified using various laboratory tests, which are as follows:
Chemical Composition Test: This test involves verifying the chemical constituents present in the cement. These are the primary factors that directly influence the properties and behaviour of cement during hydration and setting. The components include iron oxide, magnesium oxide, silica, alumina, and others.
Consistency Test: In this test, the cement is mixed with water at a specific consistency and spread over the glass plate. After 24 hours of curing, the consistency is evaluated to identify whether the cement has achieved the desired properties during this setting period.
Fineness Test: The fineness of cement is a significant factor that plays a vital role in the strength-gaining speed, hydration, and heat evolution during the process. Generally, finer particles are more effective in accelerating strength development. Unfortunately, excessive fineness powder has the drawback of premature deterioration and air setting.
Heat of Hydration Test: During the cement hydration process, a certain amount of heat is released. Measuring such heat is essential to avoid temperature-related issues, particularly in massive structures like high-rise buildings or dams.
Setting Time Test: The setting time of cement is measured in two variations: initial setting time and final setting time.
- Initial Setting Time – This refers to how long the cement paste maintains its elasticity after mixing with water. It is important for transportation, handling, and the placement of mixtures.
- Final Setting Time – This involves calculating the time taken from when water mixes with cement to when the paste loses its elasticity. This timeframe helps manufacturers determine whether the cement can withstand external forces and harsh weather conditions.
Soundness Test: The soundness test identifies any expansion that has been made in the cement after setting. Because it leads to poor structural integrity and disruptions in the hardened mass. This expansion is primarily caused by improper mixing of raw materials, inadequate burning, or insufficient fineness of grinding.
Strength Test: The strength of the cement cannot be defined directly. Instead, by evaluating the compressive strength of the mortar, you can gauge the strength of cement at a specific period.
Tensile Strength Test: This test takes place in a tensile testing machine. The cement-sand mixture is prepared with 8% water content and poured into a briquette. The mixture is then heated at a temperature of 25 or 29 degrees Celsius for the next 24 hours. The average tensile strength is then recorded after 3 and 7 days.
How to Check the Quality of Cement Before Taking It into the Construction Site?
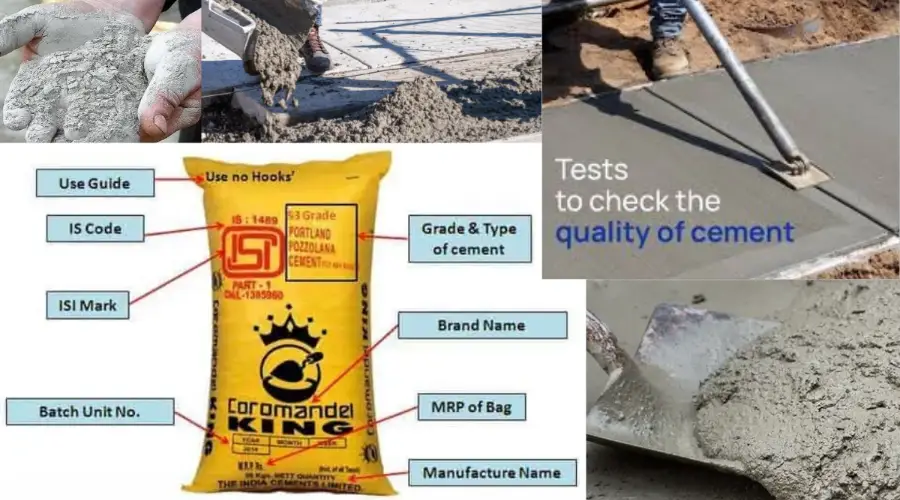
Cement is a primary construction material used all across the world. The quality of this material is crucial to ensuring the overall strength and stability of the structure. Therefore, you should be aware of certain essential components before buying, which are listed below:
Manufacturing Date
Always check the manufacturing date printed on the back of the cement bag. Generally, most people are unaware that cement loses its strength as days pass. Although it is packed inside a bag, the chemical reaction that takes place with atmospheric moisture is unavoidable. Experts suggest you buy cement packed within 90 days from the date of manufacturing.
Colour of Cement
The colour of cement helps you determine its original quality and composition. Cement is typically available in a uniform grey colour with a slight greenish shade. If you find a dark greenish colour or any other shade, it may indicate that it contains an excessive amount of lime or clay.
Presence of Lumps
Open the cement bag to ensure it does not contain any lumps inside. This is the most significant step in assessing the quality of cement. As discussed above, lumps indicate that the cement is exposed to moisture, which causes it to lose strength and stability. If you find any lumps inside, you should reject them and contact any other supplier or manufacturer.
Float Test
The float test is another simple way to identify the purity of cement. To ensure the cement is free from dust and dirt, you can take a handful of cement and drop it in the bucket of water. Good quality cement will float on water for some time, whereas cement with impurities will settle immediately. Cement mixed with dust will float on water for a longer time.
Adulteration Test
Adulteration means adding any other substances to the cement to lower its quality and improve its weight when packing. Take a pinch of cement and rub it in your fingers; if you find it smooth, you can go ahead to use it. Conversely, if it feels rough, it indicates that the cement is mixed with excess sand. Adulteration refers to the fineness test of cement.
Temperature Test
This is a simple way to assess the quality of cement at the construction site. Just put your hand inside the cement bag; if you feel cool, the bag is free from hydration, and no chemical reaction takes place. If it feels warm, you should replace it with another bag.
Strength Test
To check the soundness or strength test of cement, take a 200 mm long block that is 25 mm wide and 25 mm tall. Let it soak in water for about 7 days, and then apply the cement on the block. To verify its strength, place a weight of around 35 kg on the block. If you don’t find any cracks or damages on blocks while holding the weight, the cement is of good quality.
Odour Test
Smelling is another simple way to evaluate the quality of cement. Generally, cement is odourless; however, if you feel any earthy smell inside the cement bag, it indicates that it includes an excessive amount of sand and clay in the material.
Setting Test
Setting tests evaluate the consistency of cement while using it. You are recommended to take at least 100 g of cement and mix it with water on a glass plate. Ensure the paste is like a cement cake with straight edges, and then submerge the glass plate into the water for about 24 hours. If you find the cement cake remains the same without any cracks or spots, it indicates the cement is of good quality.
How to Check the Quality of Cement On-Site?
Good quality cement is a way to enhance the life of a structure. It is absolutely essential to conduct these easy steps on-site before using it in the construction.
Smell Test: Cement is odourless; hence, if you detect any earthy smell from the bag, it indicates compromised quality. It is advisable to replace the bag with another; otherwise you can contact another supplier or manufacturer.
Shape Test: Cement is a smooth and fine grey powder with a slight greenish shade. If you find any lumps inside the bag, it could indicate the mixing of sand or any other impurities. A smooth texture is an identification of pure cement and has a consistent composition.
Strength Test: The strength test evaluates the compressive strength of concrete. This test involves applying a load to cement mortar until failure. This load sequence must take place in no less than 20 seconds and no more than 80 seconds.
Consistency Check: Cement must maintain a standard consistency to achieve the desired strength and durability. The test involves mixing the cement with water and heating it at a constant temperature of 25 degrees Celsius. After curing, the quality cement retains its original shape and gains some strength.
Final Wordings
Cement quality is a prime factor in obtaining the desired strength and durability in all construction projects. It can be determined using various parameters, some of which are explained in this aforementioned article. Understanding these properties can help you make informed decisions when purchasing for your construction.