Natural cement is stronger than conventional cement, with higher compressive and tensile strengths than Portland cement. It is environmentally friendly, consumes less energy in the production process, and helps to lower the carbon footprint. Natural cement is a revolutionary product in the cement market that can considerably reduce carbon emissions and provide stronger and more resilient construction material. This natural cement is genuinely green and does not pollute the environment in any way. Let us delve deeper into the manufacturing process, properties, and applications of natural cement.
What is a Natural Cement?
Natural cement is a binding material derived directly from naturally occurring argillaceous limestone, which contains clay. This unique material has no additives and includes all the properties of cement, which is used for concrete, plaster, and mortar.
Natural Cement provides a variety of environmentally friendly mortars, grouts, and shotcrete with a reduced carbon footprint that is ideal for several construction projects. This product is perfect for projects that need quick serviceability because they are naturally waterproof, chemically resistant, and offer quick strength gain with short curing durations.
Historical Origin and Spread:
The production and use of natural cement began in France and England and eventually made its way to the United States. It was utilised in well-known national monuments and infrastructure projects, including the Erie Canal, Brooklyn Bridge, Washington Monument, and the U.S. Capitol. Additionally, it was utilised for smooth external stuccoes, cast embellishments, and mouldings in upscale residential and commercial buildings.
Raw Materials Used in Natural Cement
The only raw material that can produce natural cement is argillaceous limestone (which contains clay). During the production process, nothing is added or nothing is removed from the argillaceous limestone. Additives are not required during the production of natural cement. They are solely excavated from the earth, heated, and then powdered to use as cement.
You can use this natural cement as a base and add any other minerals or additives that suit your construction needs. Natural cement is not a new material but has been around for years. The Romans are famous for using this natural binder in their construction. While using limestones in the construction process, they mix a pozzolanic material, a primary deposit of volcanic ash, which activates the limestone for faster setting as well as provides high strength for the structures. Likewise, in India, we use clay instead of pozzolanic material.
Manufacturing Process of Natural Cement
Raw materials and chemistry:
A particular kind of limestone called clayey marl (marlstone), which has impurities that have accumulated over geologic time, is the source of natural cement. These marls have a considerable quantity of alumina in addition to amorphous silica, which is similar to natural hydraulic limes.
The process of burning:
When the marl is burnt slowly at temperatures below 2200°F, CO2 is released from the limestone. Like natural hydraulic limes, the leftover quicklime (CaO) reacts with silica to form belite, a type of calcium silicate responsible for the slow-setting properties of natural cement. In parallel, a variety of calcium alumina compounds that are specific to natural cement are created when quicklime and alumina react.
Final Product and Grinding:
Natural cement is made by grinding the clinker or burnt materials into a fine powder. To create the finished product, this powder can be combined with water and aggregates.
Configuring Properties:
Because of the quick setting characteristics brought about by the alumina reaction with water, which happens in minutes as opposed to hours or days as with hydraulic limes, natural cement differs from hydraulic limes. The high binding strength of natural cement gives more options for the kinds and quantities of aggregates that can be employed than pure lime or hydraulic limes.
Comparing This Material to Others:
Natural cement and gypsum plasters have similar fast-setting properties, although they differ chemically. Natural cement’s special chemistry makes it more versatile in construction applications and offers improved binding strength.
Properties of Natural Cement
Early Compressive Strength: Because of the initial calcium aluminate set, natural cement has a rapid increase in compressive strength.
Low Permeability: It is perfect for some stone applications because of its low permeability, which prevents water from penetrating.
Compatibility with Natural Hydraulic Limes: These binders are compatible since they have a comparable chemistry and a long-term silicate curing pattern.
Enhanced Durability: Natural cement improves compressive strength and resistance to cold, salt, and erosion, and decreases permeability and shrinkage when combined with natural hydraulic limes.
Applications in Historic Restoration: Because of its historical use, it is frequently used in restoration projects, especially when it comes to classic architectural forms and craft processes.
Flexibility with Aggregates: Rich mixes that may provide fine detail in moulding and ornament casting are possible because aggregate utilisation is not unduly restricted.
Aesthetic Applications: It creates long-lasting and visually appealing stucco with integral colouring when mixed with natural hydraulic limes.
Applications of Natural Cement
Natural cement stones are the source of natural cement-like Medina cement, Puzzolana cement, and Roman cement. They are primarily involved in the rail, civil engineering, construction, water, and utility industries. The wide range of applications of natural cement are as follows:
Concrete Repairs
- Natural cement provides versatile solutions for concrete repairs such as structural and cosmetic issues, applicable to vertical, horizontal, and overhead surfaces, including bridges, sea defences, potable water systems, lintels, and floors, using hand application or spray techniques.
Waterproofing and Rendering
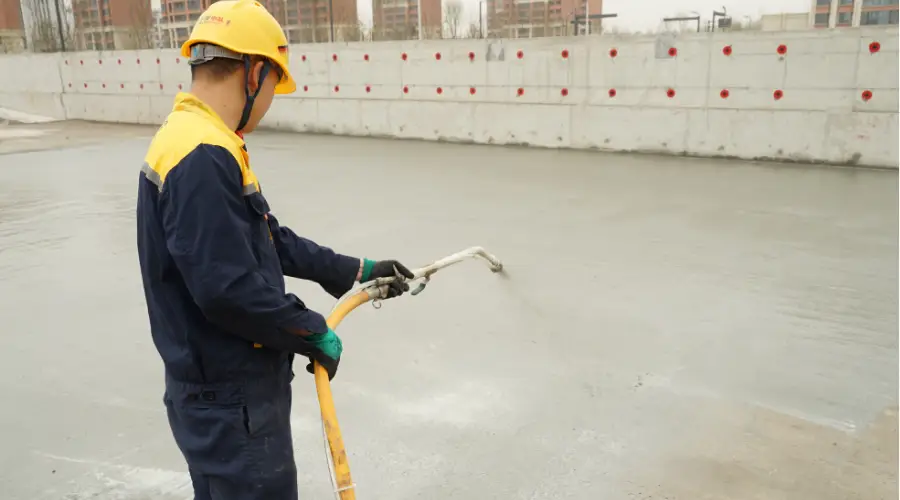
- Natural cement offers solutions for areas requiring a rendering system, protection against positive and negative water pressure, and applications such as basements, cellars, lift pits, swimming pools, tanks, tunnel linings, and leak sealing.
Grouting
- Natural cement is suitable for grouting applications due to its rapid setting and strength gain, chemical resistance, suitability for potable water, and versatility in stabilisation, void filling, and tunnelling projects.
Screeding
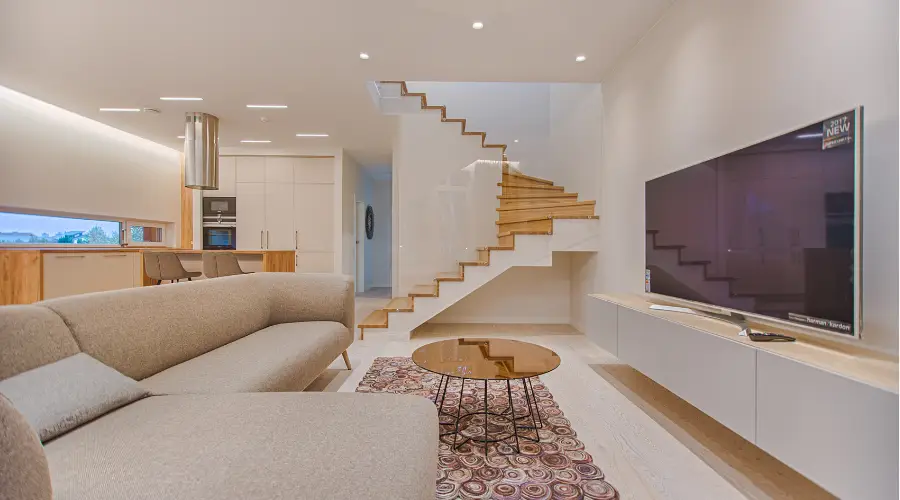
- Natural cement is ideal for screeding in applications requiring a quick turnaround, offering no curing period, overcoating within 1 hour after setting, and suitability for pools, balconies, potable water, areas prone to chemical attack, and the food industry.
Underwater Works
- Natural cement specialises in underwater works like concrete repairs, underground grouting and pointing, leak sealing, and general maintenance for watercourses, including potable water reservoirs, tanks, rivers, canals, coastal environments, and scour protection.
Sprayed Concrete
- Natural cement is commonly applied in dry-sprayed concrete for tunnel linings, retaining walls, ground support, underpinning, and concrete repairs, as well as in sea defences, tidal areas, and potable water-approved structures.
Natural Cement vs. Portland Cement
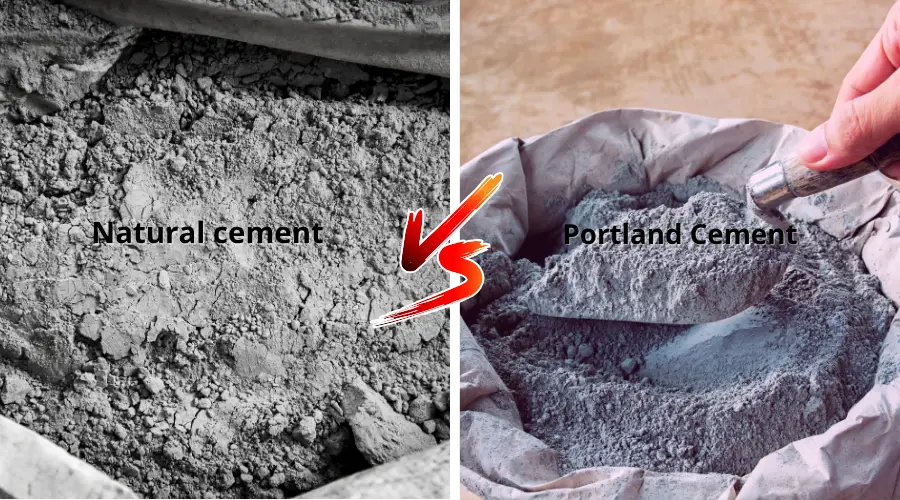
S.No | Aspect | Natural Cement | Portland Cement |
1 | Origin | First appeared in England in 1796, patented by James Parker | Developed in 1824 by Joseph Aspdin |
2 | Raw Materials | Marl (75-60% carbonates, 25-40% clay) | Limestone (80-75%) and clay (20-25%) |
3 | Manufacturing Temperature | 800–1200°C | >1300°C |
4 | Manufacturing Duration | 8–20 hours | <8 hours |
5 | Hydraulic Properties | Rapid-setting (<12 hours) | Slower-setting (>1 hour) |
6 | Types | – Rapid Natural Cement (RNC)- Slow Natural Cement (SNC) | N/A |
7 | Mineralogical Composition | Major: C2S (dicalcium silicate)Minor: C3S (tricalcium silicate), gehlenite | Major: C3S (tricalcium silicate)Minor: C2S (dicalcium silicate), gehlenite |
8 | Setting Time | RNC: <30 minutesSNC: 30 minutes–12 hours | >1 hour |
9 | Strength & Hardness | Lower strength and hardness than Portland cement | Higher strength, rigidity, and hardness |
10 | Durability | Less durable than Portland cement | More durable, water-resistant |
11 | Applications | Ports, channels, drains, water supply networks | General construction, buildings, bridges, roads |
12 | Compatibility in Restoration | May be incompatible with modern cement due to differences in strength and permeability | Often used in modern restoration, but can cause incompatibility with old materials due to higher rigidity and impermeability |
Conclusion
Natural cements are still important for the preservation and restoration of old buildings, even if Portland cement has mostly superseded them in contemporary construction. It’s important to identify the conflicts of modern cement and carefully consider how they work with contemporary materials while renovating older structures. Maintaining the integrity of structures constructed using natural cement requires an understanding of their characteristics and historical background.