Off-site construction techniques are becoming increasingly common for building and renovating commercial projects to cut costs and improve efficiency. In-plant or off-site techniques can also address ongoing industry issues such as the scarcity of trained staff, rising costs, and limited materials supply.
For example, the cost of timber tripled at the start of 2022, which put a lot of pressure on architects, builders, and other industry participants to reduce costs and increase efficiency wherever possible.
Off-site construction can help reduce these problems, but it can also be more work up front for the contractors and project owners, which can be unsettling. Many projects will find that the benefits of offsite building methods greatly outweigh the additional coordination required, even with this departure from the status quo.
Brick & Bolt provides everything you need to know about permanent off-site construction, along with a list of its main benefits, things to think about before you begin, and advice on including project stakeholders.
What is Offsite Construction and Pre-Fabrication?
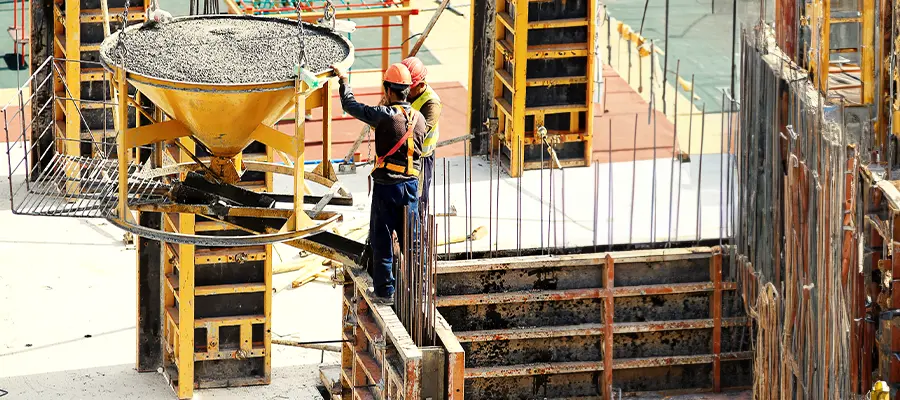
Pre-fabrication and off-site construction entail creating a building partially or entirely in a factory before being delivered and installed at the project site.
This method builds the modular elements off-site while enabling site development activities (excavation, concrete foundation, etc.) and the installation of structural elements to proceed. Building multiple sections simultaneously shortens the project’s total completion time in all weather conditions.
Types of Off-site Construction
Off-site construction can be divided into two primary categories:
- 2D modular wall panels finish the structure’s interior and exterior walls.
- 3D volumetric modular modules, full rooms or portions of a building.
2D Modular Wall Panels:
In a factory, 2D prefabricated panels, or prefab walls, are assembled into layers for simple transportation and installation on the construction site. Continuous insulation (CI), weather barriers, drainage, window and door apertures, structural steel framework, and other system components can all be found in prefabricated wall panels. To speed up the dry-in process, exterior insulation and finishing systems, or EIFS, are offered as panels. Similarly, insulated wall panels, which can be applied to interior or external walls, are frequently used to expedite and simplify insulation.
Architectural wall panels, often known as panelised facades, are the outside treatments found on prefabricated walls in buildings. These systems, like the Modulite CI panels from Dryvit, can overload a structure, minimise thermal bridging, and provide a personalised facade with infinite finish possibilities for new construction and external repairs.
Labourers affix the panels to the structure’s exterior after the components are brought to the construction site. This method allows interior trades to finish their job sooner since contractors dry in the structure more quickly than they would during regular construction. The final installation should account for the additional time needed on-site for electrical, plumbing, and HVAC services, as these are typically ongoing in the factory. Here is more information regarding the advantages of CI panels.
3D Volumetric Modular Modules
Larger, three-dimensional rooms or a group made at a factory before delivery are known as 3D modular units. 3D volumetric units are very efficient and can be the most economical choice for new buildings, especially in repeating assemblies like apartments and hotel rooms, thanks to the front-end production process. This does not imply, however, that each module’s design, inside and external finishes must be the same. Unit-to-unit variations in these designs allow for the creation of any desired building look.
Due to their size, 3D modular modules require more expensive transportation to their intended location. Every state has unique shipping regulations, so a route must be planned well before the “oversize load” leaves the factory.
When compared to traditional on-site building and the use of 2D panels, the assembly process is typically less labour-intensive once the cargo arrives. These specifics can be evaluated and taken into consideration throughout the design stage.
Utilising a Hybrid Method of 2D Panels and 3D Modular Construction
Off-site construction is not a binary choice. Hybrid models are feasible and typical, with certain building components completed on-site and others built in a factory. The optimal mix of panelisation, modular construction, and conventional building techniques will depend on each project’s design, schedule, and worksite circumstances. Using them all may be more effective in certain circumstances. For example, common spaces of a hotel or office building could be built on the spot, with the building façade installed as panels and the individual rooms delivered as 3D pods.
A mixed-use structure is another illustration of a hybrid construction model. The lower one or two stories of a “podium building” are constructed as a concrete podium and include amenities like parking garages or retail businesses. These elements are made on-site to form the building’s foundation. Subsequently, modular homes are built on-site and later stacked for residential use atop the podium. To meet the requirements of almost any project, a plethora of off-site and traditional construction combinations are possible.
Advantages of Offsite Construction
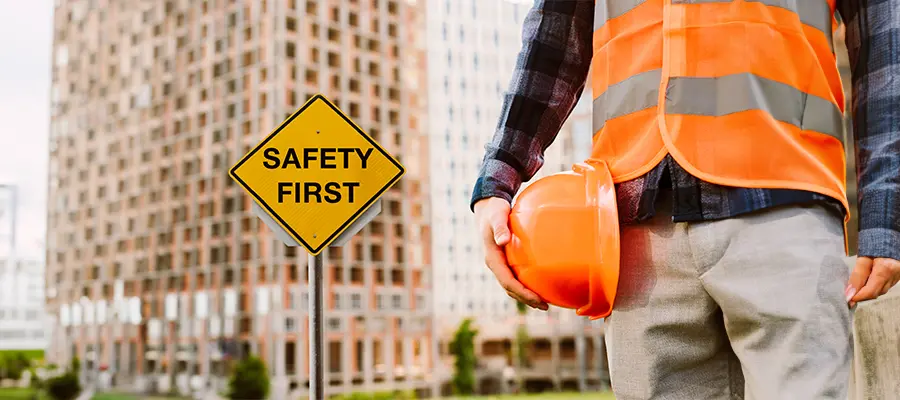
Offsite construction is becoming increasingly popular as more businesses realise the advantages of relocating the building process from the actual site to a controlled factory setting. Here, we examine some factors that make remote computing the newest big thing.
Safety
Compared to the actual construction site, which is subject to weather and visibility variations, the factory presents a far more predictable environment. When the conditions are constant throughout, errors are significantly less frequent. The factory is not affected by the majority of the most hazardous construction site risks, such as falls from great heights and machine mishaps.
Effectiveness and Stability
Because off-site construction ensures consistency, it can be completed in less time each time. As long as the project is not delayed by mitigating factors like inclement weather, work may be certain to be completed on schedule and to the highest possible standard.
Durability
Less energy and large machinery are needed for off-site construction. In addition to using fewer cars to transport the completed product to the site, there is less waste because the company may purchase materials in bulk and determine their requirements more precisely.
Higher Quality
Prefabricated construction is primarily a repeatable procedure that increases quality control and lowers the likelihood of errors, rework, and callbacks. Furthermore, because off-site components must endure the shocks and strains of shipping, they are frequently built with even greater durability than on-site components, even if they are naturally built to meet or exceed building requirements. All stakeholders benefit from increased quality assurance, which ensures a long-lasting, robust outcome.
Lower Labour Costs
Research has indicated that erecting a factory structure requires much less labour. According to the Steel Construction Institute (SCI), the hands needed for a four-story residential development might be lowered by up to 75%. These savings would also apply to other types of construction. Naturally, the corporation will pay lower wages if fewer employees exist.
Reduction in Training
Acquiring the skills necessary to do a job well in an offsite build is far easier and requires less time than training people to be experts in onsite construction. Building is effectively turned into a manufacturing process when the construction process is moved to a factory, where each worker simply needs to understand their specific, tiny job on the assembly line. Quicker delivery and cost savings are achieved with less training.
Reduced Construction Schedule and Shorter Install Time
Fewer parts of an off-site construction project are weather-dependent because most of the work is completed indoors. Factory-built components can be finished at any time of year, regardless of external weather conditions.
Furthermore, panels and modular pieces are assembled simultaneously when on-site work starts. Before beginning further work, concrete must typically be cured for at least 28 days in the building industry. During those 28 days, work in a factory might continue by utilising off-site construction. To help shorten the project’s overall timetable, everything is taking place at the same time. Since most liquid elements, such as sealants and air barriers, have already been cured and won’t be impacted by fluctuating temperatures or precipitation, the units can be placed on-site in a wider range of climatic conditions once finished in the factory.
Things to Think About Before Selecting Off-Site Construction
While the procedures for on-site and off-site building methods are similar, they also call for careful planning and coordination.
Making Decisions Early
Everyone involved will observe that more decisions must be made at an earlier level because modular fabrication proceeds swiftly and frequently in tandem with other stages of the construction process. Furthermore, modifications are easier to make once work is underway.
Choose an off-site construction business with experience to help with this. They should be able to identify the decisions that need to be made, set up a schedule, and effectively oversee the entire process.
Financial Difficulties
The parties must also agree on who is responsible for the financial and insurance commitments of the prefabrication process. Regarding the lender’s definition of “property,” the financing may present difficulties. Lenders frequently withhold cash until the units are delivered to the job site, even when they are still in the factory.
Developers and building owners who require up to 50% of the loan upfront may find this troublesome. For their unorthodox construction approach, looking to nontraditional financiers, such as real estate investment funds, is advised.
Many funding options for off-site construction for Deep Energy Retrofit projects and building renovation for increased energy efficiency are available. Commercial Property Assessed Clean Energy, or C-PACE, is one such option. Under this scheme, energy upgrades or renewable energy systems for commercial buildings can be funded and repaid through property tax assessments.
Additionally, many states offer specialised funding for deep retrofit projects, such as RetrofitNY, Clean Energy Works Oregon, and Efficiency Maine’s PACE Loan Program. To promote retrofits in private residences, social housing, and community facilities, the Federation of Canadian Municipalities (FCM) recently introduced three new funding initiatives in Canada, totalling an expenditure of nearly $1 billion.
Design-Related Issues
Does this project lend itself well to panelised or modular design and fabrication? Each job will be unique. For example, the time and cost advantages associated with off-site building might be less significant in places with consistent or favourable weather and easy availability of raw materials. Before choosing, it is useful to perform a cost-benefit analysis of both possibilities. Furthermore, traditional on-site construction better fits complicated buildings without recurring components.
Anything from wall panels, precast concrete, permanent modular building systems, and more can be constructed off-site. Any architectural structure with recurring characteristics, such as restrooms, dormitories, or patient rooms in a hospital, may find it a feasible alternative. Offsite construction is enjoying a rebirth, but it’s nice to know you may still achieve your specific objectives while picking the benefits of this cutting-edge method. When the time comes to start building, remember that a design-build team can assist you in pursuing every avenue of offsite construction while seeing your commercial project through from conception to groundbreaking.
No Interruption to the Occupants
For those unfortunate enough to live nearby, an onsite development can be a tough test of patience. Construction and delivery vehicles travelling to and from the site can impede access routes and parking spaces, creating noise and air pollution from heavy gear and equipment. This is a specific issue in confined urban settings. Furthermore, cranes and construction sites are always ugly and can be a nuisance for a long time. Locals will be relieved to see development moved into a factory away from the site.
In conclusion, off-site construction is a revolutionary change from traditional building methods. It has many benefits, such as higher efficiency, lower prices, and greater sustainability. Offsite construction includes a wide range of new methods that change how buildings are planned and built. These methods include modular construction and prefabrication techniques. Offsite construction can help the construction industry be more productive, complete projects better, and meet the growing needs of the built environment if people in the industry understand its principles, methods, and benefits. Offsite construction isn’t just a trend; it’s a must for the future of construction. It makes better, faster, and more environmentally friendly buildings possible.