One common building material that can be utilised in contemporary construction is precast concrete. It is generally created in a controlled environment, often away from the construction site or in a factory. It is resilient to severe weather and long-lasting. The primary advantage of this precast concrete is its recyclable property. It is changing how structures are built from a fastened construction process and lower labour costs to higher design customisation and flexibility.
So, suppose you are looking for an advanced construction material that fastens your project timeline, cuts down labour costs, and has flexible design work. Because of its endurance and structural integrity, precast concrete is a good option in that situation. All of the manufacturing techniques, uses, varieties, and advantages will be covered in this blog to assist you in making your own choice.
What is Precast Concrete?
Precast concrete, a modern building material, can be created at a large factory or industrial facility by pouring concrete into a mould rather than on-site. The factory-made precast concrete can be transported to various places where it is required. As a completed material, the cured concrete product can be effectively placed on the construction site.
Manufacturing Process of Precast Concrete
Moulds can be used to create precast concrete. These moulds can be reused. Concrete can be cast into a reusable mould to create precast concrete, which is then delivered to the construction site. It shortens the construction timetable, improves quality control, and makes the process more efficient. Several key steps can be followed in manufacturing precast concrete. Let us discuss the process below:
- Design and Mould Preparation
The initial step in preparing precast concrete involves creating reusable moulds designed for multiple castings.
- Concrete Mix Design
Certain characteristics of the concrete can be enhanced by several components, such as cement, sand, water, aggregates, and some artificial additives.
- Batching
Each component is carefully measured and allowed for mixing in a batching plant. The consistency and quality of the final concrete material can be managed well through this process.
- Casting
The mixed concrete is poured into moulds, shaping it into the desired precast component. To enhance the final product’s strength, reinforcements like steel bars or mesh may be embedded within the mould.
- Curing
To increase its strength and durability, concrete undergoes a curing phase after it is placed. This process is often carried out in a controlled setting, such as a water bath or curing chamber, to give the best conditions for hydration.
- Demoulding
The precast materials are removed from the moulds after reaching the setting time and hardened state. After cleaning, the moulds are ready for the subsequent casting procedure.
- Finishing
These precast elements need additional finishing processes to achieve their appearance and functionality. They include treating the surface for its smooth appearance; polishing and coating can be done.
- Transportation
Specialised vehicles can be used to transport these precast concrete materials due to their challenging properties, such as huge size and careful handling. It requires a lot of attention while transporting the precast concrete materials from the factory to the construction site.
Materials Used in Precast Concrete
A precast concrete construction is made up of numerous components. Among these resources are:
Cement: This is the most crucial component of precast concrete. To produce high-quality precast concrete as an NPCA-certified plant, you must meet the standards specified by the National Precast Concrete Association.
Precast concrete typically incorporates ordinary Portland cement (OPC) in grades 43 and 53, while Portland slag cement and Portland pozzolana cement are often used for precast concrete in challenging environments, such as tidal areas.
Water: A great precast concrete mix design is largely dependent on the ratio and cleanliness of the water. Impurities must be absent from the water because they can lower the quality of the mixture.
SCMs, or supplemental cementitious materials: They are usually industrial byproducts and sometimes natural materials that possess cement-like qualities. These materials are blended with ordinary Portland cement to enhance its hydration qualities.
Aggregate: The mix design for a particular precast concrete construction usually determines the type of aggregate to be used. Usually, a project manager will take texture, colour, and durability into account. It is possible to employ a special aggregate.
Precast concrete can also contain the following additional materials:
- Water-resistant additives
- Oxides
- Reinforcement bars
- Steel tendons
- Joints
- Lightweight combinations
- Non-shrinkable fibres
- Epoxy Grouts
Types of Precast Concrete Products
Five typical varieties of precast concrete are as follows:
- Precast Concrete Walls
Precast concrete walls are well suited for creating low-maintenance structures that withstand poor climatic conditions. They can also be used to create interior and exterior surfaces to save time and money.
- Precast Concrete Beams and Columns
Precast concrete beams and columns are ideal for different kinds of structures, from mid-level apartments to commercial buildings. They are available in various shapes and sizes and can be flexible for project requirements. They are easily installed and have high structural strength for bearing heavy loads. Vibration and moisture do not affect them.
- Precast Concrete Slabs and Planks
The heavier precast concrete slabs are generally flat and rectangular and can be widely used for flooring, roofing, and walls. Large areas can be spanned by installing planks.
- Precast Concrete Stairs
Precast concrete stairs are fast-moving precast concrete products that can be employed for emergency exit stairways as they are easy to install and save time. The stairs are made with treads and risers as per project specifications.
- Precast Concrete Retaining Walls
These concrete retaining walls are manufactured to form a seamless barrier and are engineered to interlock with one another. They are often reinforced with galvanised steel or enhanced with admixtures or fibre reinforcements for additional strength and durability.
Application of Precast Concrete
- Precast concrete can be used for traffic barriers, stairs, columns, paving slabs, and architectural veneers in single-level to multi-level parking facilities.
- Commonly used in residential and commercial buildings for walls and floors, offering energy efficiency and moisture resistance.
- They are included as compound walls for property division, sound walls for noise reduction, and retaining walls for structural support in various settings.
- Precast concrete is essential for bridge components like beams, arches, and deck slabs, as well as culverts for wastewater and stormwater management.
- They can be used in water and wastewater management systems that include septic tanks, catch basins, manholes, and stormwater systems for safe containment and pollutant removal.
- Precast concrete protects utility connections with products like vaults, light pole bases, transformer pads, and telecommunications systems.
- They are suitable for agricultural applications because of their durability against extreme conditions, being used in feed troughs, fencing, bunker silos, and livestock management systems.
- Precast concrete is found in roads, railways, and airports for barriers, underpasses, railroad ties, and tunnel segments.
- Modular and decorative products include paving in customisable textures and colours, building components, and site features like cladding and mantels.
- Marine and hazardous containment can be made using precast concrete, such as seawalls, docks, vaults, and hazardous material storage, offering resilience against natural and manmade forces.
Advantages of Precast Concrete
Faster Construction: Precast concrete speeds up the building process as ready-made components are delivered and installed, eliminating on-site curing delays.
Higher Strength: Precast concrete uses well-mixed materials, ensuring greater strength and durability compared to site-cured concrete.
Controlled Production: Manufactured in controlled environments, precast concrete is not affected by weather conditions like rain or humidity, ensuring consistency.
Superior Quality: Dedicated production facilities focus on quality control, resulting in uniform and reliable products.
Cost Savings: Faster construction reduces labour costs and minimises resource wastage.
Design Flexibility: Specialised reusable moulds allow for intricate shapes, sizes, and decorative designs that are difficult to achieve on-site.
Precast Concrete vs. Cast-in-Place Concrete
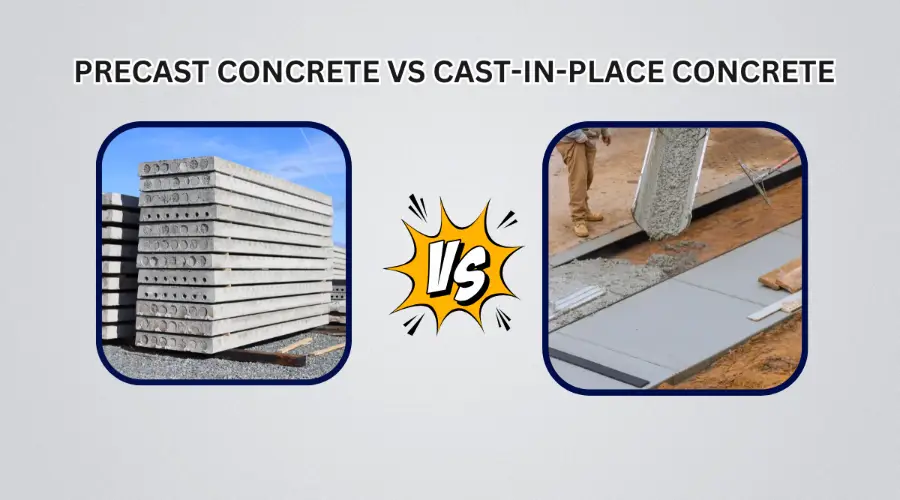
S.No | Criteria | Precast Concrete | Cast-in-Place Concrete |
1 | Location of Casting | Manufactured off-site | Poured and moulded on-site |
2 | Level of Quality Control | Produced in a controlled environment | Subject to imperfections on-site |
3 | Customisation | Less customisable, suited for repetitive elements | Greater customisation is ideal for complex structures. |
4 | Production Time | Faster to produce | Their production time is longer due to setting and curing time on site. |
5 | Cost | Typically higher due to the manufacturing process | This can be higher due to specialised equipment and skilled labour. |
6 | Best Use | Suitable for mass-produced elements (e.g., walls, columns) | Preferred for larger, complex structures, or challenging sites |
Conclusion
Precast concrete provides quick construction, higher strength, and uniform quality through regulated manufacturing methods. It guarantees cost savings and lessens weather-related delays. Its adaptability in design makes elaborate forms and ornamental elements feasible. In conclusion, precast concrete is a cost-effective, long-lasting, and adaptable option for a wide range of building projects.