Prefabricated wall panels are building products made off-site and assembled on-site. They are constructed using standardised measurements and materials, enabling fast installation. Depending on the intended look, strength, insulating properties, and fire and moisture resistance, among many other reasons, these panels can be made of different materials and are suitable for a wide range of places, from hospitals and hotels to private houses.
In this article, you will learn the advantages of using prefabricated wall panels as well as the factors and difficulties that you should consider in choosing the best option for your project.
What are Prefabricated Wall Panels?
Different portions of the walls that can be constructed under a controlled environment with exact measurements are termed prefabricated wall panels. According to their intended usage, a manufacturer has to expertly design, measure, cut, and assemble each piece without any damage. These wall panel components are manufactured in a setting where each portion has to be produced in a controlled environment, rather than being framed and constructed on the construction site. After production, the panels are then transported to the construction site for further installation processes.
Manufacturing Process of Prefabricated Wall Panels
Prefabricated wall panels employ high-quality materials such as sheathing, engineered timber, and dimensional lumber. They have been assembled in a controlled atmosphere at a separate production centre to guarantee a high-quality product. The time and energy required to construct wall panels on-site can be saved by producing them in this controlled environment around the clock.
Some businesses may use professionals who have been carefully educated to use the newest technology to enable simplified manufacture, delivery, and installation of every prefabricated wall panel in addition to offering a superior product that is economical and saves time on projects.
Properties of Prefabricated Wall Panels
Because of their dependability and efficiency, prefabricated wall panels are frequently utilised in construction. Important characteristics include:
- Sturdy: Designed to endure and withstand challenging circumstances.
- Accurate: Featuring smooth finishes and exact measurements.
- Insulated: Make sure there is adequate sound and heat insulation.
- Adaptable: Capable of fitting many finishes, sizes, and designs.
- Eco-friendly: Use sustainable products and cut down on waste.
- Cost-effective: Quicker production and installation save time and money.
- Lightweight and strong: Very strong but simple to install.
- Enhance building safety by making it fire-resistant.
- Stay strong throughout time by being resistant to moisture and pests.
- Easy to Install: Faster building thanks to pre-made components.
Benefits of Using Prefabricated Wall Panels
Prefabricated wall panels offer utility to every building project, be it residential or commercial. The benefit of using a prefabricated wall panel lies in its ability to enable the building project to meet tight deadlines and expenditures. Since panels are built to specifications according to a particular job, construction professionals do not have to rely on wasted material, shortages, and weather delays. Additional benefits of wall panel components include:
- Allowing construction to continue without interruption.
- Respecting strict budgets
- Providing a high level of durability and quality
- Accurately designed wall panels
- Making the workplace safer
- Ensuring a smooth and rapid installation
- Cutting down on project waste
- Assisting in the fight against labour shortages in building projects
Applications of Prefabricated Wall Panels
The following uses for prefabricated wall panels are very advantageous:
- Building with multiple families
- Construction of new homes
- Garage additions to homes
- Stables, barns, and additional outbuildings
Installation of Prefabricated Wall Panels
Prefabricated wall panel installation is a simplified procedure that drastically cuts down on labour expenses and construction time. This is a detailed tutorial on the standard installation procedure:
1. Site Preparation
A survey needs to be conducted to make sure the installation location is stable and level. To support the panels, a strong foundation is needed. Depending on the project, a concrete slab or footing is typically used for this.
2. Panel Delivery:
Off-site production of prefabricated panels is followed by their transportation to the construction site. Larger or heavier panels may require specific transporting techniques, and the panels are usually transported in bulk. Based on their size and weight, panels are carefully unloaded and staged for installation using forklifts or cranes.
3. Lifting and Positioning
Cranes or other heavy machinery are used to raise large panels into place. It is possible to raise smaller panels by hand or with mechanical support. The panels are set and aligned as per the architectural plan. A great deal of care is taken to ensure that the panels fit exactly into their assigned locations.
4. Securing the Panels
The panels are bolted, screwed, or welded to the foundation or existing structures. Joints are sealed to avoid moisture or air leakage, and gaskets or sealants are applied for a secure fit.
5. Bond Strengthening
Additional reinforcements, for example, in the form of steel brackets or reinforcement bars are added to fortify the bonds between panels. Temporary braces will sometimes be installed to support panels while permanent bonding is made to secure the entire structure.
6. Finishing Sealing Gaps:
Gaps between the panels and surrounding surfaces are sealed for tightness and weather resistance. Finishing treatments like painting, texturing, or cladding are applied based on the panel type (concrete, steel, or composite).
7. Inspection and Quality Check
The final examination is carried out to ensure that the panels are firmly in place, properly aligned, and free of installation flaws. The strength and durability of the installed panels are verified to ensure they can support the planned loads and environmental factors.
8. Final Touches:
After panel installation, additional work like plastering, painting, and insulation may be done. Plumbing, electrical wiring, and other utilities are also installed as needed.
Cost Analysis of Prefabricated Wall Panels
This simple comparison table shows the differences in price for prefabricated and traditional wall panels in India. Keep in mind that these prices may fluctuate based on region, quality of materials, and specific needs for the project.
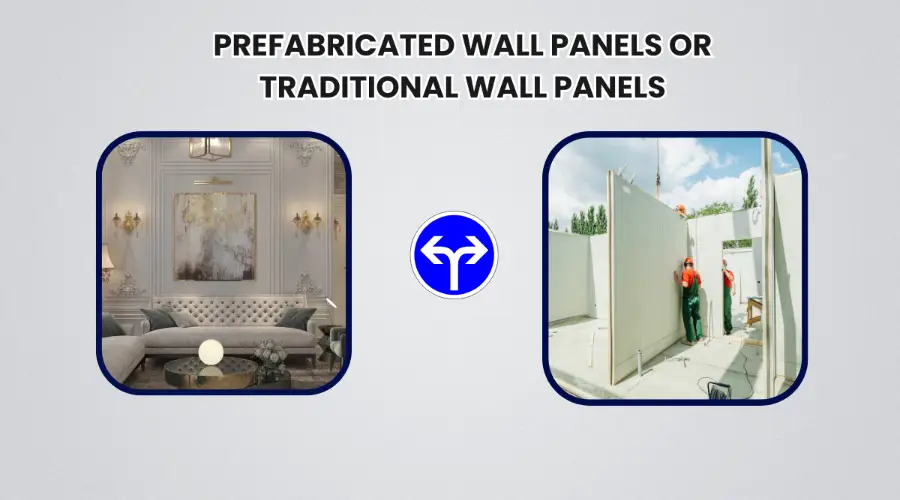
S.No | Cost Factor | Prefabricated Wall Panels | Traditional Wall Panels |
1 | Material Costs | ₹450 – ₹700 per sq. ft. | ₹300 – ₹500 per sq. ft. |
2 | Labour Costs | ₹100 – ₹150 per sq. ft. | ₹250 – ₹400 per sq. ft. |
3 | Installation Costs | ₹50 – ₹100 per sq. ft. | ₹150 – ₹250 per sq. ft. |
4 | Transportation Costs | ₹10 – ₹20 per km (for bulk delivery) | ₹5 – ₹15 per km |
5 | Project Duration (per sq. ft.) | 30-50% faster installation | Standard duration |
6 | Maintenance (Annual) | Low (minimal upkeep) | Medium to High (depends on material) |
7 | Energy Efficiency Savings | High (insulated panels) | Medium (depends on material) |
8 | Customisation Costs | ₹100 – ₹300 per sq. ft. | ₹50 – ₹100 per sq. ft. |
Conclusion
Prefabricated wall panels have revolutionised commercial construction by making the building process easier. Their benefits include faster construction, consistent quality, reduced waste, and improved environmental sustainability. They also offer architectural flexibility and enhance safety on building sites. In fact, this adaptability has clear benefits for building owners as well as developers and builders, who stand to earn enormously.