In the construction sector, cement is considered the primary binding component of concrete. You can plan to build a house, a strong bridge, or any other project; the base material used to build all these is cement. Cement alone is not adequate, but the right cement.
To that, it becomes very imperative to understand the properties of cement for engineers, architects, and builders so that the quantity and quality of their work could be assured. The article covers some key properties of cement and their effective application in order to satisfy the requirements of modern construction.
Physical Properties of Cement
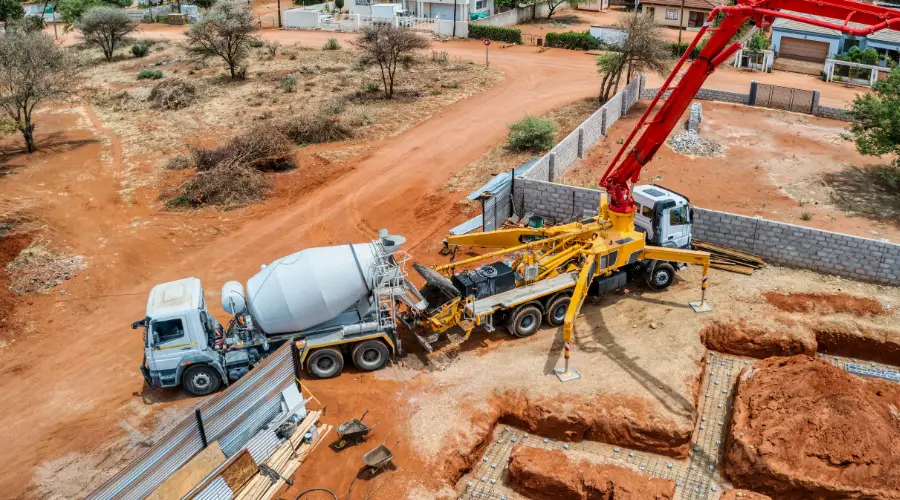
While it is a first-to-go construction material in a checklist, it has various physical properties you haven’t heard of before.
Fineness of cement
Fineness of cement refers to the particle size distribution of the cement particles. It is a measure of how finely the cement has been ground during the manufacturing process. Usually, it is measured in square centimeters per gram (cm²/g), or as the percentage of cement retained on a standard sieve.
Finer cement particles have a larger surface area available for hydration, leading to faster chemical reactions and quicker strength gain. According to IS recommendations, the fineness of cement should be below 10%.
In another way, we can test through the Blaine test, which allows a certain quantity of air to pass through the bed of cement particles.
By this test, the cement particle size is determined by the rate of airflow resistance.
Soundness
Soundness of cement refers to its ability to retain its volume after setting, ensuring that the hardened concrete or mortar remains stable and does not undergo expansion or contraction over time. This property is crucial because any excessive changes after setting can lead to cracking, warping, or disintegration of the concrete structure.
The main cause of this dimensional stability is when excess free lime above the normal level is combined with acidic oxide at the kiln. Another reason can be the high presence of magnesium or calcium sulphate.
Here’s where you need to consider the soundness of cement.
To check this, you can use two traditional methods while purchasing:
- Le Chatelier Test and
- Autoclave Expansion Test.
In the Le Chatelier Test, ordinary Portland cement should not expand more than 10 mm according to ASTM C151 or IS 4031 Part 3.
The autoclave expansion test for ordinary Portland cement shall not show an expansion of more than 0.8% as per ASTM C151 or IS 4031 Part 3.
Consistency
More elaborately, the consistency of cement refers to the ability of cement to mix with water and give out a homogenous paste. This provides strength in concrete structures.
The perfect consistency of the mix is provided by the accurate water-to-cement ratio. A high water-cement ratio results in a more fluid paste, while on the other hand, a lower ratio results in a stiffer paste.
It should be noted that different water contents are needed to yield standard consistency for various types of cement, like ordinary Portland and rapid-hardening cement.
The Vicat apparatus can typically be used to undertake the standard test to determine the consistency of cement paste. This will outline its fluidity and plasticity.
Strength
Cement has the ability to withstand axial loads. A proper volume of cement mixed with materials impacts a load bearing capacity of the concrete which provides compressive, tensile, and flexural strength.
The proportions of compounds like C3S (tricalcium silicate), C2S (dicalcium silicate), C3A (tricalcium aluminate), and C4AF (tetracalcium aluminoferrite) can affect strength development.
However, the use of relevant chemical and mineral admixtures can enhance or modify the strength rate of cement.
Setting time
Setting time refers to the periods a cement paste takes to change from a fluid or plastic state into a rigid state.
Setting time of cement therefore refers to the two periods namely;
Initial setting, and Final setting.
i) Initial Setting Time
The time from the addition of water to cement until such time when the paste starts losing plasticity is what we call, the initial setting time. During this stage, further methods of molding or shaping can be done.
For Ordinary Portland cement(OPC), the initial setting time should not be less than 30 minutes.
ii) Final Setting Time
The final setting is a period of time from the addition of water to cement; the paste at this moment has lost plasticity and is hard enough to resist a certain load.
The ideal value for the final setting time for OPC should not be more than 600 minutes (10 hours).
Heat of hydration
When cement comes into contact with water, exothermic chemical reactions liberate the heat.
The reaction is significant in the setting and hardening process of cement. Evolved heat may raise the temperature of concrete, which affects the performance and durability of the concrete structure as a whole.
The products formed in these reactions give cement its strength.
Higher C3S and C3A content increases the heat. The presence of gypsum affects the reaction of C3A, controlling the heat release.
Both these ingredients produce less heat during hydration.
Loss of Ignition
A cement sample on heating at 900 – 1000°C loses weight. This loss of weight on heating is computed as loss of ignition.
Poor or adulterated during transportation or transfer the material may undergo pre-hydration or carbonation, both of which may be reflected by increased loss of ignition.
Chemical Properties of Cement
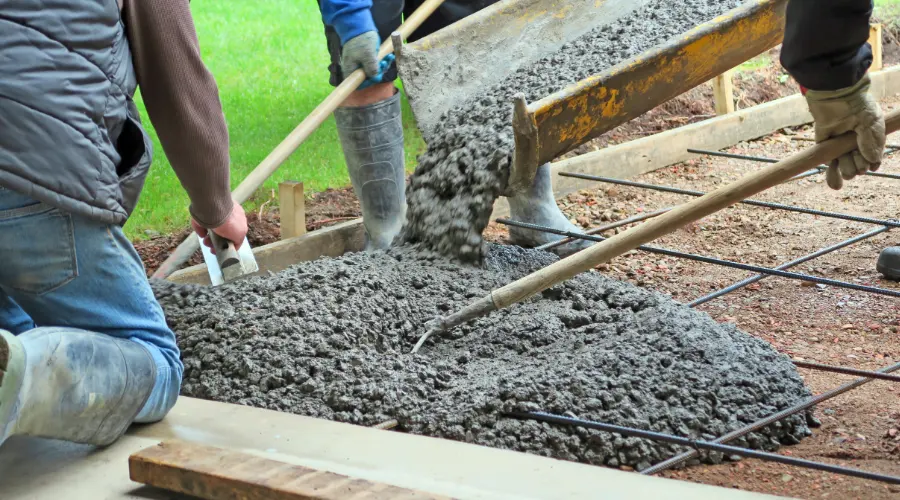
The much needed raw material for cement production is limestone.
It is largely made up of calcined, sand or clay, bauxite and iron ore; it may include shells, chalk, marl, shale, slates, clay and blast furnace slag.
Chemical analysis of these cement raw materials provides ample information about the chemical properties of cement.
Tricalcium aluminate (C3A)
The low content of C3A makes the cement sulphate-resistant.
Gypsum reduces the hydration of C3A, which evolves a large amount of heat at the beginning of hydration. C3A does not contribute more than a few per cent of strength. There are two types.
Type I cement: It contain more than 8% C3A and has up to 3.5% SO3. The higher sulphate content helps to control the hydration process of the high C3A content.
Type II cement: It contains less than 8% C3A and has up to 3% SO3. This lower sulphate content is suitable for the lower C3A levels, helping to maintain appropriate hydration control and contributing to moderate sulphate resistance.
Tricalcium silicate (C3S)
It reacts quickly with water, releasing moderate heat. It is responsible for early strength gain and structural integrity. About 45-60% of cements comprises of C3S.
Dicalcium silicate (C2S)
In contrast with tricalcium silicate, C2S is responsible for early strength gain. Calcium Silicate in cement helps the strength gain after one week. This improves the resistance to chemical attacks and comprises about 15-30% of cement.
Ferrite (C4AF)
Ferrite is a fluxing agent which gives colour to cement. It reduces the melting temperature of the raw materials in the kiln from 3,000°F to 2,600°F.
Though it hydrates rapidly, it does not contribute much to the strength of the cement. Also, it provides lower heat of hydration when compared to C3A and C3S which typically comprises 8-12% of cement.
Magnesia (MgO)
The manufacturing process of Portland cement uses magnesia as a raw material in dry process plants. Small amounts are good to consider, whereas excessive MgO can lead to expansion and cracking.
It is mandated to keep the MgO content below 6%.
Sulphur trioxide
A high amount of Sulphur trioxide can make the cement unsound, requiring more setting time than usual. To make this efficient, 1-2% of SO3 is acceptable.
Iron oxide/ Ferric oxide
Iron Oxide or Ferric oxide is known for its contribution for colour to cement. It is responsible for formation of clinker compunds like Tetracalcium Aluminoferrite(C4AF) and other properties such as setting tie, heat of hydration and workability. By knowing the amount of Fe2O3 in the cement mix, one can produce high quality cement with desirable outcomes.
Conclusion:
More than having knowledge about the cement and its usage, understanding its properties is essential to ensure the quality, durability and performance of concrete structures. Above discussed physical and chemical properties play a crucial role in its application and effectiveness.