Recently, PVC roofing sheets are gaining popularity in the Indian construction industry. Made from polyvinyl chloride, these sheets are known for their durability, low maintenance and versatility. Manufacturers engineer them in such a way that it can withstand harsh weather, UV exposure and other environmental conditions. With all these qualities, these sheets are some of the most preferred choices for industrial and residential applications. Despite being lightweight, their sturdy nature simplifies the installation process, providing optimum roofing solutions for various types of buildings.
Covering everything from manufacturing, the various types available to the advantages and disadvantages, this blog explores everything you must know about PVC roofing sheets. Whether you are a homeowner looking to install the sheets for your new home, or a construction professional looking to install them in your commercial, industrial and home renovation projects, read this guide to get a comprehensive understanding and make an informed decision.
PVC Roofing Sheet- What Is It?
Polyvinyl Chloride, abbreviated as PVC, is a synthetic plastic polymer used in numerous applications, including roofing. Manufacturers design PVC roofing membranes by bending PVC with other additives and reinforcing materials. These together form a strong flexible and highly resistant material, making an excellent roofing choice for residential and commercial buildings. The sheets include a single-ply membrane with two layers of vinyl bonded to a polyester scrim layer.
Since these roofing sheets deflect intense UV rays, manufacturers paint them in white or other lighter shades. Compared to other traditional options like metal panels and concrete roofs, these innovative roofing systems are easy to install.
Composition of PVC Roofing Sheets
During the manufacturing of PVC sheets, vinyl resin is compounded with plasticisers, ultraviolet light inhibitors, heat stabilizers, biocides and colour pigments. The membranes generally consist of a polyester reinforcement scrim that the manufacturers place between two layers of PVC material. The single-ply top membrane contains additives that make it resistant to UV rays and prevent curing. Manufacturers make the bottom ply (the ply facing the roof) with black PVC. The ply mostly consists of plasticizers as they boost flexibility. However, it does not contain any other fillers or additives.
PVC Roofing Sheets: Types
People use roofing sheets and membranes for numerous reasons. While some use them to enhance the aesthetic value, others install them to protect their homes from external weather conditions, including torrential downpours, snow and heavy winds. The level of protection offered by a plastic roofing solution depends on the combination of material used by the manufacturer. These roofing solutions come in the following varieties.
Corrugated Roofing Sheets
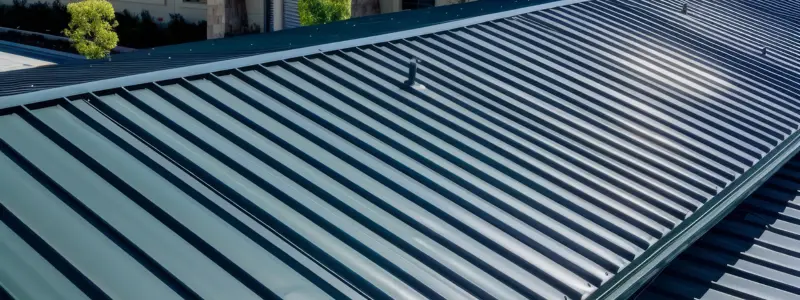
It is one of the strongest roofing sheets available in the market. The sheets are suitable for agricultural buildings, garages and industrial sheds and have one of the best life spans. Unlike flat roofing sheets, the corrugated roofing sheets do not get damaged easily. They can be further classified into the following:
- Bitumen: Besides being lightweight, bitumen coatings offer excellent resistance to water. Therefore, they find the best use in garages, sheds and agricultural buildings.
- PVC Plastisol: The sheets are highly resistant to scratching and damage. Though they have a life span of 20 years, they can last over 40 years with proper maintenance.
- Polyester-painted sheets: These sheets are highly suitable for agricultural buildings, as they have high resistance to scratching and damage.
Flat Roofing Sheets
These sheets find the most use in industrial complexes and commercial buildings. Flat PVC sheets are popular for their durability and can withstand frequent exposure to extreme temperatures and weather conditions. Besides, they require low maintenance, making them an ideal choice for warehouses, manufacturing facilities and multi-store retail complexes.
Apart from these two major shapes, PVC roofing sheets are also available in various other forms which can also be customised based on individual project needs and desires.
Manufacturing of PVC Roofing Sheets
Raw Materials Required
These include the following:
- Vinyl chloride monomer: The solution, also known as VCM, is obtained from the reaction between chlorine and ethylene and is the essential building block of PVC.
- PVC Resin: It forms by polymerizing vinyl chloride molecules, forming the base structure of your PVC roofing solutions.
- Plasticizers: Manufacturers add them to the resin to enhance its flexibility and workability. Although most manufacturers use phthalate-based plasticizers, bio-based plasticizers are becoming popular due to environmental concerns.
- Stabilizers: They help prevent PVC from degrading during the manufacturing process. They offer thermal stability to the sheets and prevent oxidation.
- Fillers and Pigments: Manufactures add various fillers and pigments to enhance specific properties or to add colour to the sheets.
The Manufacturing Process
The manufacturing of the PVC profile sheet involves a systematic process, where the manufacturers ensure the product’s quality and characteristics at the end of each stage. The process involves the following stages:
Polymerisation
It’s the first step in creating the PVC roof sheet design. The vinyl chloride monomer at this stage undergoes a process known as polymerisation. Here several VCM molecules link together to form a polymer chain, which the manufacturers achieve through either emulsion polymerisation or suspension polymerisation.
Producing the PVC resin
PVC resin is obtained in the form of small particles after polymerisation, which most manufacturers refer to as PVC resin granules. The granules serve as another base material of the sheet.
Compounding
It forms the next step, wherein the manufacturers mix the resin with various additives to improve its properties. They mix the additives like pigments, stabilizers, fillers and plasticizers in measured quantities. They then blend them together with the resin to create a homogeneous mixture.
Extrusion
Once the PVC compound is ready, manufacturers feed it into an extruder, a machine responsible for melting the mixture to form a uniform molten mass. The manufacturers forces the molten PVC through a die, imparting a desired shapes and thickness to the sheet. The sheets go through either flat-die extrusion or calendaring depending on the type of sheet manufactured.
Cooling and sizing the sheets
After extrusion, the new and fresh roofing sheets undergo cooling and solidification. Proper cooling is essential to prevent warping and deformities in the final product. The manufacturers then trim the sheets and cut them to the required dimensions.
Embossing
Have you ever noticed a specific texture or pattern on the sheets’ surface? These sheets undergo a process called embossing to produce such patterns, which involve embossing rollers that press the desired design onto the sheet during the cooling process.
Surface treatment
It is an optional process. During the process, the PVC sheets undergo a special treatment that enhances their properties. Surface treatments often include corona treatment to improve printability. The manufacturers apply a special coating to boost the sheet’s chemical resistance.
Quality control
During the manufacturing process, the manufacturers employ strict quality control measures, ensuring the sheets meet the required specifications and standards. The sheets undergo various tests, including checking of tensile strength, tear resistance and thickness measurements that ensures the sheets’ qualities.
Packaging
After passing the quality checks, the manufactures engage in packaging the sheets. It prevents the sheets from damage during transportation and storage. With proper packaging, you can prevent any damage or contamination that could affect the sheet’s performance.
Installation Process of PVC Roofing Sheets
Installing your PVC roof on your building involves a systematic process. These include:
Planning and Preparation
Before installing the roof, you must plan and prepare in advance. It starts with analysing the condition of your current roof and determining whether PVC roofing is ideal for your building. After analysing the condition, calculate the quantity of materials required for the installation. These include PVC sheets, adhesives, fasteners and flashing.
Removal of Existing Roofing
If your roof already has a roofing solution, you first need to remove the existing roofing. This includes repairing the damages of the underlying structure. It’s a labour-intensive process and requires careful attention so that the roofing you install does not cause further damage. Look for the presence of debris and leftover materials and clean them thoroughly. Inspect the surface for any unattended imperfections that might affect the installation. With proper preparations, your new roof will provide optimal performance and longevity.
Install the Insulation
After removing the old and damaged roof, it’s time to install the insulation on the roof deck. Proper insulation helps improve energy efficiency, reducing the heating and cooling costs of the structure. Choose the best quality insulation materials that are compatible with vinyl roofing systems. When installing the insulation, ensure to secure it well to prevent gaps and air leaks that often undermine the effectiveness of the insulation. It helps maintain a consistent interior climate, prolonging the lifespan of your roof.
Installing the PVC Sheets
Once you install the insulation, it’s time to fasten the membrane. You need to start by rolling out a complete roll of the selected PVC roofing sheet. Now, first fasten one end of the sheet by holding the material straight and tight. This minimises the wrinkles on the roll. Next, roll out the second sheet to overlap the fasteners installed along the previous sheet. Repeat the process. Once you fasten the sheet with the seams, you can weld them with a hot air welder to form one monolithic sheet.
Adding Finishing Touches
Your roof installation ends with adding flashing around the edges and penetrations such as chimneys and vents. Flashing prevents the entrance of water at vulnerable points of the roof. Finally, you must inspect the roof carefully for the presence of gaps and imperfections. Add any required final changes, such as gutter installation.
Advantages of PVC Roofing Sheets
With PVC roofing, you get numerous benefits. Here’s what makes the material one of the most preferred options for roofing:
Energy Efficient
The material’s effective properties reduce the amount of heat absorbed by a building, thereby keeping your interiors cooler. It reduces your energy bills, minimising the strain on coolers and air conditioners.
Durability and Longevity
Another significant advantage of PVC roofing is its durability. With proper maintenance, a PVC roof can last between 20 and 30 years. It can withstand a variety of harsh weather conditions, including high winds, heavy rain and even hail.
Low Maintenance
Another significant property of these roofs is that they require low maintenance. Your PVC roof panels require only routine inspections and occasional cleanings to keep the roof in top conditions.
Chemical Resistance
Most commercial and industrial settings have high exposure to harsh chemicals. In such a setting, PVC roofing is an ideal choice. The material is highly resistant to such elements, making it a durable option for such an environment.
Disadvantages of PVC Roofing Sheets
No roofing material is perfect, and it’s the same with PVC sheets as well. When you are aware of the challenges, you make an informed decision. The following are the drawbacks of choosing PVC profile sheets as your roofing solution.
Environmental Concerns
Since PVC is synthetic plastic, its use raises numerous environmental concerns. During the production of the material, the manufacturers use fossil fuels that generate numerous by-products. However, you can recycle the material, helping mitigate the environmental impact.
Initial Cost
These sheets have a higher cost compared to the traditional roofing system. However, the long-term benefits the sheets offer, including energy efficiency and low maintenance often justify the initial investment.
Temperature Sensitivity
PVC is highly sensitive to extreme temperature fluctuation, preventing it from expanding and contracting. Despite the good thermal stability, proper installation is crucial to prevent issues related to temperature changes.
PVC Roofing Sheet Price
A PVC roofing membrane might cost around INR 100 and 1000 per square feet, depending on the type. However, when installing PVC sheets on your roof, you must understand the factors that impact the overall material cost. Enlisted are some of these factors
- Raw materials: The price of the primary component- polyvinyl chloride resin affects the overall cost.
- Transportation and logistics: The distance between the manufacturing unit and the project site affects the transportation costs. The logistics expenses include mode of shipping, freight fees and fuel prices.
- Installation requirements: The complexity of your roof’s design and the specialised labour required for the right installation adds to the project cost.
Conclusion
With a durable, cost-effective and versatile solution for various building projects, PVC sheets have revolutionised the industrial roofing landscape. However, when installing your PVC sheets do not forget to assess your requirements and budget.
As a leading construction firm in India, Brick & Bolt aims to provide design-build services on all your projects. Whether you are building your dream home, redesigning your existing home or want to install a new roofing solution, the professionals associated with the organisation make the process smooth, memorable and efficient. With real-time data tracking, transparent communication, quality checks and regular updates on your projects, the organisation promises to bring trust into the informal field. Contact Brick & Bolt today to build your dream home!