Construction projects require quality management as a basic component. In addition to meeting the client’s initial expectations, it guarantees that the project’s final structure is safe for operation and complies with building standards. A strong management system in the construction industry must include Quality Control (QC). Delivering top-notch structures that satisfy design and legal requirements requires the implementation of efficient quality control procedures. This article explores the definition of quality control in construction, its importance and quality control methods in brief. Read on to learn more.
What is Quality Control in Construction?
The process of quality control in civil engineering or construction involves examining building operations, materials, and craftsmanship to find and address violations from the established criteria. Product-focused quality control makes sure that the finished product satisfies all the necessary requirements. This includes testing materials, inspecting the location, and confirming that the craftsmanship meets acceptable tolerances.
The purpose of construction quality control (QC) is to ensure that project deliverables fulfill the needs and specifications of the client through a series of procedures and actions. Monitoring and testing are done to find problems and make sure that quality requirements are met.
Quality control, according to ISO 9000, is “a component of quality management focused on fulfilling quality requirements.” It is an organized method for making sure that building operations, supplies, and craftsmanship meet the needs of the customer. Through tests, assessments, and inspections, its primary goal is to find and fix problems during the construction phase.
Is Quality Control in Construction Necessary?
It is important to ensure that the construction quality is good, which can be achieved by adopting quality control measures during the construction process. Let’s explore how quality control impacts construction:
Guarantees Safety and Structural Integrity
By making sure that the materials and craftsmanship fulfill predetermined criteria, quality control measures help prevent building failures. Cracks, structural collapse, and durability problems are less likely to occur as a result.
Conformity to Rules and Guidelines
Local and international standards like ISO 9001, ASTM, ACI, and BIS must be followed, and quality control makes sure that structures are constructed according to these standards hence, avoiding legal problems and project delays.
Economic Viability
Significant cost reductions result from the implementation of efficient quality control standards, which also lessen rework, material waste, and construction delays.
Improves Client Satisfaction and Reputation
In addition to increasing commercial opportunities, delivering high-quality projects improves a company’s brand and fosters client trust.
Makes Construction More Durable
Through quality construction, it is ensured that structures last for the expected duration, and also the cost of maintenance and repairs is lowered.
Construction Quality Control Methods:
Construction quality control management can be achieved by different methods, each with unique advantages and disadvantages based on the demands and size of a company’s projects. The ISO 9001 quality control standards were created by the International Organization for Standardisation. There are four primary strategies for managing quality control in civil engineering, which are as follows:
- Constant Improvement: Emphasises the gradual, ongoing enhancement of procedures. Improvements are found using internal analytics procedures and client input.
- Kaizen: Kaizen, which translates to “change for the better” in Japanese, is a philosophy that is used in quality control management and involves always seeking out methods to improve. Gradual gains can be observed over time when all the members of an organisation incorporate Kaizen into their everyday routines.
- Six Sigma: The goal of this problem-solving methodology is to proactively detect and address emerging problems. ‘Define’, ‘Measure’, ‘Analyse’, ‘Improve’, and ‘Control’ are the key components of this quality control management strategy.
- Lean Administration: The two main components of this strategy are waste reduction and elimination. Waste refers to unnecessary procedures and materials that don’t add value for clients or building firms.
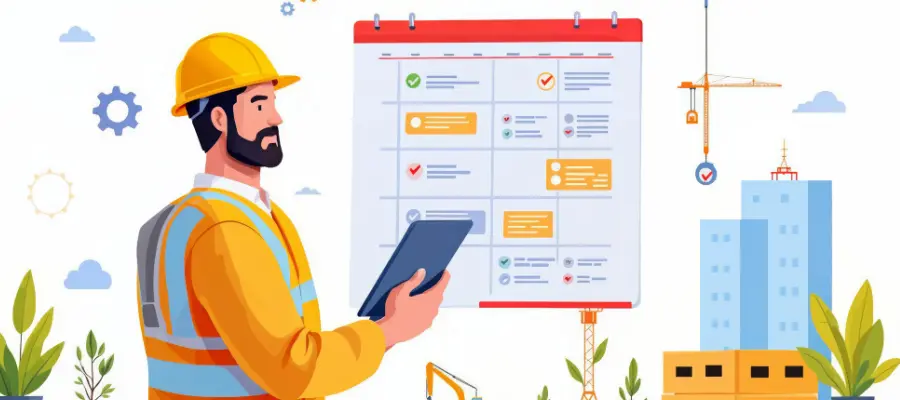
Tips for Implementing Quality Control in Construction:
Definitions of construction quality control differ slightly throughout organisations. However, while putting quality control methods into practice, all experts in the construction sector need to keep the following points in mind:
Specify the Requirements and Standards for Acceptance
Quality control standards must be well-defined prior to the implementation of quality control processes so that everyone involved is aware of what the client anticipates from the final structure. Key acceptance criteria, like finishing a project flawlessly and in accordance with client requirements and legal norms, should be part of these requirements.
Make a Plan for Inspections
Regular inspections should be conducted at various stages of the construction process as part of a comprehensive quality control plan. However, it is important that companies develop a plan outlining what needs to be examined and what constitutes an acceptable outcome, prior to conducting any inspections. All finished projects should satisfy customer requirements, business standards, and any additional suggestions made by involved parties.
Make a Quality Control Check List.
It might be challenging to manage and communicate quality control expectations and requirements among teams in the absence of a uniform quality control checklist. By making sure that important aspects of quality control are not missed, a checklist streamlines the inspection procedure. Checklists also make it easier to express issues and the precise duties assigned to each member of the construction process.
Correct Errors or Shortcomings
The goal of putting quality control procedures into practice is to guarantee that building projects satisfy customer requirements and ensure safety. The most crucial part of any quality control management strategy is probably providing the time and resources needed to fix errors and address shortcomings as they appear. Regular inspections and ongoing team and construction site monitoring provide opportunity to identify subpar work before it is finished and delivered to the client.
Examine and Evaluate Issues as Well as their Fixes.
Along the journey, challenges and problems will be discovered while tracking progress and examining the construction. Along with addressing these difficulties when they emerge, it’s a good idea to give construction project managers a way to evaluate the success of each job and determine how to prevent similar issues in their subsequent projects. After decisions are reached on these matters, quality control managers must inform the whole team of any potential changes to the standards and expectations for future projects.
Conclusion:
The significance of quality construction is well known. In construction, quality control methods not only reduce the possibility of delays. It also guarantees that their expectations and criteria will be met by the project. Conducting inspections of the tools and materials utilised in the project is one popular quality control procedure in the construction industry.
To guarantee the durability, security, and effectiveness of civil engineering projects, quality assurance and control are crucial. Construction reliability is increased, standards’ compliance is guaranteed, and faults are reduced by putting strong quality control measures into practice. With careful design, highly qualified workers, and contemporary technology, the construction sector can provide infrastructure that is both affordable and long-lasting.
Brick & Bolt, a leading construction company in India, conducts 470+ quality checks on every project. A specialised system called QASCON is utilised by a team of construction experts, providing assured quality control. Apart from this, a 10 year structural warranty is provided to address any concerns that may arise. Contact Brick & Bolt today to build your dream home with the best quality!