In modern construction, lightweight structures that can be erected quickly play an important role. Materials that facilitate this kind of construction must have a good strength-to-weight ratio, while cost effectiveness would be another crucial benefit. One material that ticks all these boxes is a sandwich panel, whose popularity is widespread in the construction industry. Read on to learn what a sandwich panel is, its features, types, benefits in buildings and cost.
What is a Sandwich Panel?
A sandwich panel is a composite material consisting of three layers- a thick, lightweight core attached to two thin but stiff skins. In common terms, a low-density core (such as rockwool or polystyrene) is ‘sandwiched’ between two high density outer layers (such as wood or metal sheets) to form a sandwich panel. Relatively cheaper core materials are used to provide strength and hold all the layers together, creating a stiff panel that can be employed as a part of roof and wall structures in buildings.
How is a Sandwich Panel Made?
Sandwich panels are generally made in large manufacturing plants. Here, the two outer layers are fed into a machine where they are clamped with their inner sides facing up. They are then treated to high frequency pressure to clean out dirt and grease and to apply an adhesive uniformly. Protective films are layered onto these sheets before the core material is placed and fixed to them using adhesives. The composite panel is then passed through a heated drying tunnel, where the core is allowed to expand to its full size and obtain the necessary strength. After this, the panels are cut into the required sizes, becoming usable sandwich composite panels.
Types of Sandwich Panels
A sandwich panel can be made with different materials that form both the exterior and core layers. Based on the material composition, some of the commonly available types of sandwich panels are:
EPS Sandwich Panel
An Expanded Polystyrene (EPS) sandwich panel consists of two galvanised, weather-proof, colour coated steel/ fibre reinforced plastic (FRP) sheets sandwiching a polystyrene layer in the center. Such panels are relatively fire and moisture resistant. They are available in thicknesses of 50-200 mm and in various colours that can also be customised. EPS panels may have a smooth surface or corrugations and can be used for making both roofs and walls.
PU Sandwich Panel/ Sandwich PUF panel
A Polyurethane sandwich panel has a layer of rigid polyurethane foam sandwiched between two layers of stiff metal or fiberglass. It is also commonly referred to as a PUF (polyurethane foam) panel and is one of the most widely used types of sandwich panels. A fire-retardant chemical is often added to the foam while manufacturing to make the panel fire-resistant. PUF panels are typically available in thickness ranging from 30 mm to 150 mm.
Structural Insulated Panel (SIP)
In a structural insulated panel (SIP), the outer layers can be made of sheet metal, plywood, cement, Magnesium Oxide (MgO) board or Oriented Strand Board (OSB), while the core is made of Expanded Polystyrene (EPS) foam, extruded polystyrene foam (XPS) or polyurethane foam. Such panels are much thicker—100-300mm in thickness—than other sandwich panel types but have higher structural strength.
Aluminium Sandwich Panel
An aluminium sandwich panel has two layers of aluminium sheets sandwiching a polyurethane or polystyrene foam core. It is similar to an Aluminium Composite Panel (ACP) which has a thinner core and is commonly used for cladding. An aluminium sandwich panel can have thicknesses ranging from 10-50mm, with large lengths of upto 5m.
Rockwool Sandwich Panel
This sandwich panel has a core made of rockwool, which is flanked by two layers of colour-coated galvanised or galvalume steel sheets. Rockwool, or mineral wool, is known for having exceptional thermal and acoustic insulation properties, thus making rockwool sandwich panels ideal for various building applications. Common thicknesses of these panels lie between 50-200 mm.
Benefits of Sandwich Panels
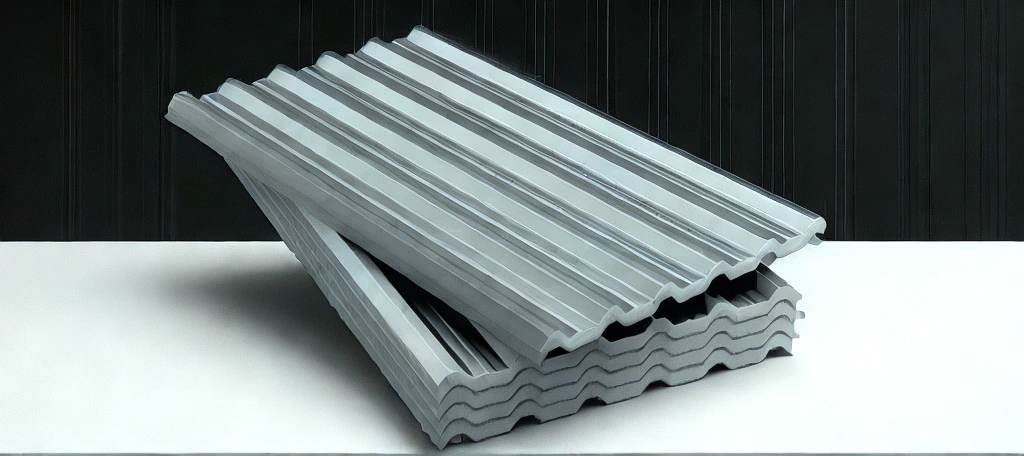
A sandwich panel offers the following advantages that make it a popular building component:
- Thermal and Acoustic Insulation: An insulated sandwich panel is sound-proof and has high thermal insulation- meaning that it can maintain controlled indoor environments.
- Lightweight: Sandwich panels have very high strength-to-weight ratios because they generally combine the best properties of different materials like metal and FRP with the core PU or EPS. The reduced structural weight resulting from the usage of these panels can reduce the overall project cost.
- Quick Installation: Sandwich roof sheets and wall panel sandwiches can be installed much faster than in-situ or precast concrete slabs and stone or brick masonry walls. Erection also is much simpler, typically only requiring screwing, bolting, welding or application of adhesives.
- Maintenance and Repair: The use of treated external layers makes sandwich panels resistant to rot, mould and moisture. However, in case of any irreparable damage, these panels can easily be dismantled and replaced.
Applications of Sandwich Panels in Buildings
A sandwich panel roof and/or a sandwich panel wall can be ideal for many building applications, including:
- Industrial buildings, where the lightweight, high strength panels can be used to construct structures with large uninterrupted spans.
- Warehouses and cold storage units: The building insulation property of sandwich panels can create an ideal temperature for storing goods.
- Temporary structures: The quick installation and easy dismantling properties of sandwich panels can aid in reducing construction timelines.
- Rooms with controlled indoor environments, such as hospitals, clean rooms and air handling units- here the air-tight property of sandwich panels is a big benefit.
- Commercial and residential buildings– for quick, cost-effective construction.
Cost of Sandwich Panels
The sandwich panel price is determined by various factors such as type, design, colour and availability. Some of the common prevailing prices in India currently are:
- Sandwich roofing sheets price (PU panel): ₹100- ₹5000 per sq ft.
- Rockwool sandwich panels: ₹200- ₹900 per sq ft. (for 50-100mm thicknesses)
- Aluminium sandwich panels: ₹100- ₹500 per sq ft. (for 10-50mm thicknesses)
- EPS sandwich panels: ₹60- ₹500 per sq ft. (for 50-200mm thicknesses)
However, these are the approximate pricess which are variable across locations and brands. Customisations in colour or increased complexity in the profile design can also mean additional charges.
Using a Sandwich Panel in Your Building
Despite the many benefits that it offers, a sandwich panel also has certain drawbacks—such as limited resistance to fire and adverse weather conditions—that hinder its usage in normal construction. Thus, its usage requires careful analysis and planning. Brick & Bolt, a leading tech-enabled company in India, offers end-to-end construction services based on the designs and experience of reputed professionals in the industry. To get your house designed and built by industry experts and know whether sandwich panels are ideal for your project, contact Brick & Bolt today!