Have you ever had pipe leaks or troubles which made you possibly sit back and wonder if you got the right joints? The truth is, that the right pipe joint selection determines the smooth operation of the plumbing system. Would you like to know which joints would fit your needs? Come, let us examine the different types of pipe joints that can protect your system and keep it leak-free!
Major Types of Pipe Joints in Construction
Threaded Joints
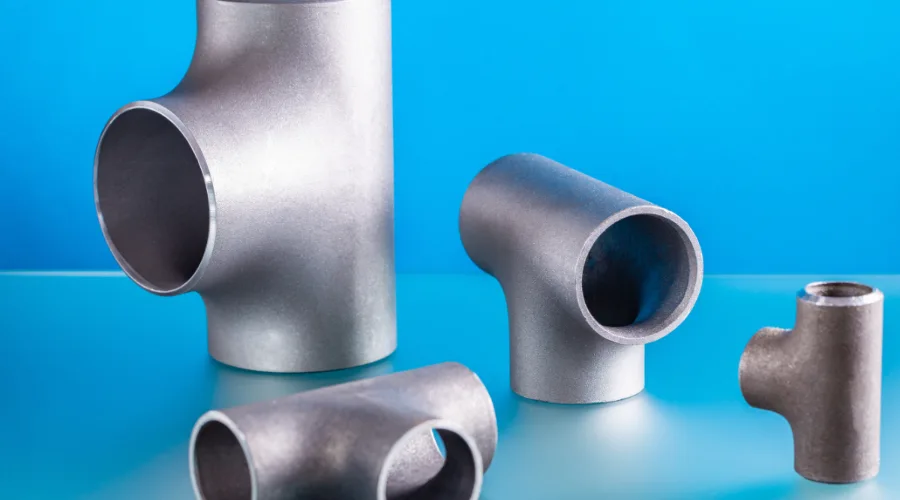
Threaded joints are among the most common joints in plumbing systems that join pipes. It includes an external component that fits the internal thread to connect two pipes. These pipes are made from metals like galvanized steel and brass. These types are used either with less internal pressure or with low temperature. These types of joints act as a simple but effective means for connecting pipes, mainly where there is a need for frequent assembly and disassembly.
Advantages
- These joints can be easily assembled and disassembled.
- These pipes are widely used and offer a cost-effective solution for piping needs.
- Often used for small to medium-sized pipes.
Disadvantages
- Susceptible to leaks, especially when threads are not properly sealed.
- They are not ideal for high-pressure applications.
Soldered Joints
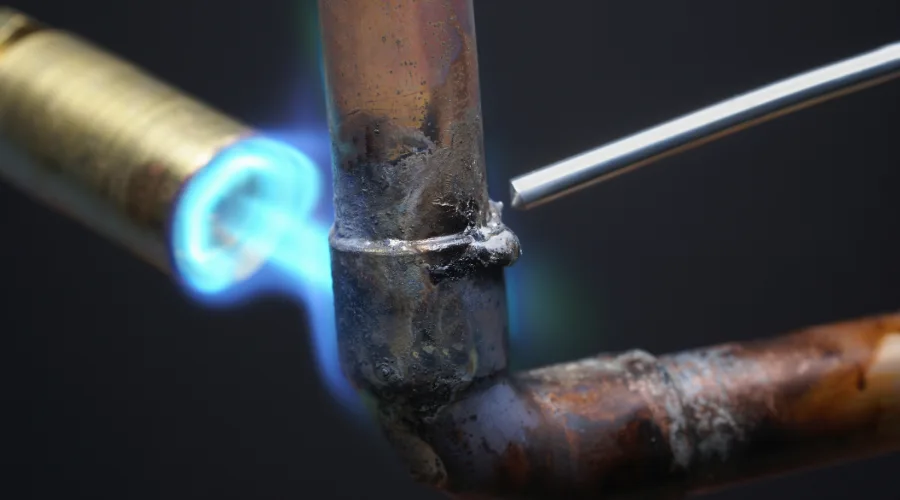
A soldered joint is a type of metal joint that employs solder as the necessary filler to create a junction between two pipes. The liquid solder is placed into an area where it meets with the other pipe so that it fits tightly onto it. Soldering is most commonly used to join two copper pipes together.
Advantages
- These joints are easy to create and don’t require high temperatures as brazed joints.
- They are suitable for small-scale plumbing systems.
- It is used to create a durable seal.
Disadvantages
- These joints are not ideal for high-pressure applications.
- These joints can be weakened over time due to thermal cycling.
Brazed Joints
Brazed joints are similar to soldered joints. They also use a high-temperature heating process, which helps melt a mostly stronger alloy of filler material for fitting the pipes. Thus, the resulting strong filler material forms a much stronger and permanent joint than that formed in the soldered joint. This technique is extensively employed for joining some metals such as copper, brass, and certain steel-related metal pipes.
Advantages
- They provide a strong and permanent connection between the two pipes.
- It does not need mechanical fasteners, as fillers itself does the job better.
- These joints are suitable for withstanding moderate pressure and moderate temperatures.
Disadvantages
- The joining process requires specialized skills and equipment.
- It requires high temperatures, which can be difficult to control.
Butt Welded Joints
A butt welding joint is the joining of two pipe ends by a full weld encircling the circumference. Here, the ends of the pipe are usually beveled with a grand good continuous weld. Butt weld joints are applicable under high-pressure-temperature conditions and provide a strong permanent connection due to their solid and smooth weld. It requires careful preparation and skilled workmen, yet it becomes very strong and durable.
Advantages
- They create a strong and permanent connection between the pipes.
- They can be used for high-pressure and high-temperature applications.
- It does not require additional components, making it last longer.
Disadvantages
- The joining process is labour-intensive and expensive, as it requires proper preparation and welding at the ends.
- It requires specialized equipment and skill to ensure that the welding is carried out properly.
Socket Welded Joints
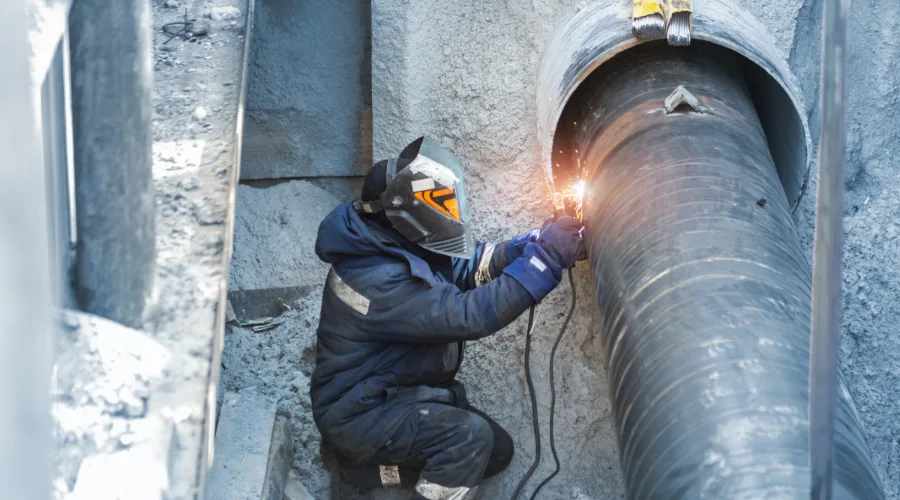
A socket welded joint is the process of inserting one pipe into the socket of a fitting and welding it all around the edge. Any small pipe is welded up to a size of 2 inches, made for systems at medium pressure. Very easy and quick in fabrication compared to butt welds; demands less labour, while there is no need for beveling of the pipe ends, but it is not as strong nor used for high-pressure applications. In certain construction setups, masonry cement is also used to fill pipe joints and protect surrounding brick or stone masonry surfaces from moisture and damage.
Advantages
- These joints are easier and quicker to prepare and weld compared to other welding joints.
- It does not require the bevelling of pipes at the end, which reduces the need for more labour.
- It can be used in smaller pipe systems where faster installation and budgets are a major concern.
Disadvantages
- These joints are not as strong as butt-welded joints, especially in high-pressure systems.
- The pipe is more susceptible to corrosion and cracking, especially under high temperatures.
Factors to Consider When Choosing Pipe Joints
Material Compatibility
Choosing an appropriate material for your pipe fittings is very important to establish durability to prevent problems like corrosion and chemical reactions, or hidden pipe damage that might require water leakage detection later on. The pipe fitting itself must be harmonically compatible with the material of the pipe. For example, a steel fitting may not be used with copper pipes, as this would lead one metal to corrode by electrical contact with the other metal, galvanic corrosion.
Pressure and Temperature Ratings
Every fitting material has its own ratings on pressures and temperatures that determine the maximum pressure and temperature the fitting can handle safely. This is very important, as pipes that are inadequate to withstand the required pressure and temperature might leads to leaks or failure of the entire system.
Pipe Size and Connection Types
Pipe sizes must be suitable for each other so that the pipe and the fittings can match perfectly. Sizes that mismatch create a perfect scenario for leaks, inefficient flow rates, or even system failure.
Flow Requirements
The purpose of the piping system, along with the flow requirements of the liquid or gas being transported, has profound implications in selecting the proper fittings. In some cases, such as bathroom layouts built over a sunken slab, proper joint selection becomes even more critical to avoid future leakages or repair issues.
Conclusion
To sum up, choosing the correct pipe joint is of utmost importance in establishing a reliable and sturdy plumbing system. Different types of joints apply for different situations regarding pressure, temperature, and material type, such as threaded, brazed, soldered, or welded. Knowledge of these options ensures that a secure connection is made and leakages are prevented, thus allowing the plumbing system to function well for many years.