Due to the increasing urbanization all over the world both in urban and rural areas, there is a huge demand for sand in construction, from concrete production to mortar creation, plastering, and even as a base material for paving. Their properties, such as size, shape, and composition, ascertain the strength and durability of any structures.
The two basically found types of sand are: M Sand (Manufactured Sand) and P Sand (Plastering Sand). Both are selected according to the construction project requirement and the quality of sand used for their final build.
In this blog, you’ll get ample information about M Sand and P Sand which helps you out what actually it is and which you can choose for your project.
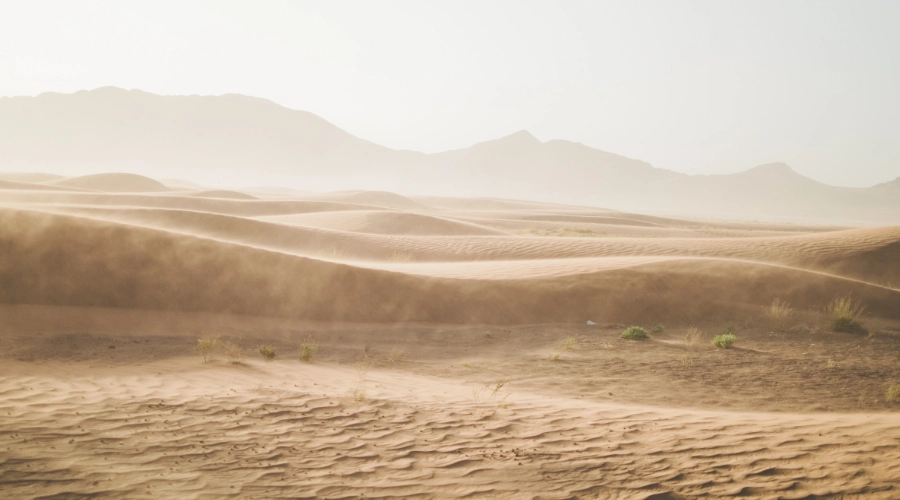
What is M sand?
M Sand, otherwise known as Manufactured Sand, is made out of hard granite stone crushed into cubical particles of small sizes. It is often used as a substitute for river sand in construction due to its quality and availability. Although it is manufactured to meet IS specifications, which a particle size should be 0 mm to 4.75 mm.
What is P sand?
P Sand is a type of manufactured sand used for plastering purposes. It has finer features compared to M Sand, giving smooth and even results on the walls and the ceiling. It is produced by crushing granite rocks and is processed to achieve a finer state suitable for plastering applications. According to IS standards, the ideal particle size should be 0.15 mm to 2.36 mm.
Three types of M Sand
Based on usage, it is categorized into three main types: Concreting, Plastering, and Brick or Blockwork.
M Sand for Concreting
The particle size of M sand for concreting shall be 4.75 mm to 3.5 mm.
In general, for building’s foundations, slabs, beams and columns are built with this specifications. The typical ratio for concreting is attained by mixing 1:2:4 that covers a initial setting time of 30 minutes and final setting time of around 10 hours. It complies with IS Code 383:1970.
M Sand for Plastering
Plastering is important while finishing the interior and exterior structures like wall, ceiling, or any other surface. A fine mixture can provide a smooth finish. For this, the particle size of sand should be taken 2.36 mm to 1.2 mm mixed with the cement in a ratio of 1:4. Also, these requirements meets the IS Code 1542: 1992.
M Sand for Brick or Blockwork
M Sand is specifically designed to provide the necessary bonding and strength required for masonry applications. Structures like building walls, partitions, and other masonry works.
Ideal particle size for Blockwork is 3.5 mm to 2.36 mm, typically mixed with cement in a ratio of 1:5 (cement: sand).
The manufacturing process of M Sand
To ensure the production of high-quality sand, M Sand manufacturing can be broken down into 5 stages.
Step 1: First, high-quality granite rocks are selected as the raw material.
Step 2: Vertical Shaft Impact (VSI) crushers are used to break stones of various sizes into aggregates then put into a Rotopactor to be crushed into sand at the correct grain size.
Step 3: After crushing, the material is screened to separate particles of different sizes. This helps in removing any oversized particles and filter uniform sand particles.
Step 4: Sand washing is done to remove tiny particles and dust. This is an important step where impurities such as clay, silt, and unwanted particles get removed from the sand.
Step 5: Grading of the final product is done to ensure that it has complied with IS standards.
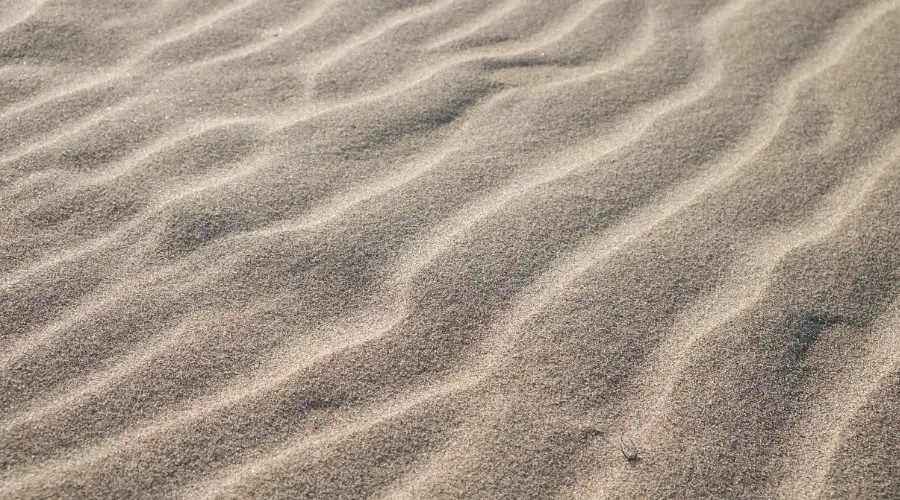
The manufacturing process of P Sand
Since P Sand is a substitute for Natural River Sand, it has to be made in such a way that the quality is comparative or better than the River Sand. Here are the exact details of the manufacturing process.
Step 1: First of all, hard rocks—either granite, basalt, or limestone—are selected free from impurities.
Step 2: The above raw materials are sent to the crushing plant wherein oversized rocks have been crushed by the primary crusher. After that, the secondary and tertiary crushers cut them into pieces of an even smaller fragment, i.e., less than 5mm in diameter.
Stage 3: Vibration screens segregate the different sizes, wherein the crushed materials are passed through vibrating screens, and the oversize goes back to the crushers for further reduction of size.
Stage 4: Water and sand washing equipment wash the material to remove impurities like clays, silts, and dust.
Step 5: Grading of the final product and, therefore, dried to remove moisture that makes it easier to store.
Which type of sand is ideal for building?
The ideal type of sand for building depends on the specific application:
- For Concreting, M Sand is first to-go for to its strength and durability.
- For Plastering, P Sand is preferred for its fine grip and smooth finish.
- And for Brick or Blockwork, M Sand provides strong bonding properties.
M sand vs. P sand
Features | M Sand | P Sand |
Particle Size | Coarser granules (4.75 mm to 3.5 mm) | Finer granules (2.36 mm to 1.2 mm) |
Application | Used for concreting and masonry work | Specifically used for plastering |
Final Outcome | Provides strength and durability | Provides a smooth and even finish |
Advantages of Manufactured Sand
M Sand has numerous advantages over natural river sand, including better consistency, higher quality, and enhanced durability for construction projects.
- It is uniform in size where the shape of particles ensures consistent quality.
- It is readily available when compared to river sand.
- More economical than river sand.
- It reduces the environmental impact caused by river sand mining.
- It is free of silt and clay particles and has denser particle packing than natural sand.
Advantages of P sand
- P Sand has better bonds with cement which increases the structural integrity of the construction.
- It is more economical than natural sand.
- It promotes sustainable construction practices that reduce the environmental impact of river sand mining.
- When compared to other types of sand, P Sand has low wastage due to uniform size and shape.
- Concrete is free from harmful materials such as clay, silt, and organic impurities, which ensures its better strength and durability.
Is M sand better than river sand?
Compared to river sand, M Sand is better in uniform quality and consistent in particle size with high-value strength.But why not River sand?
River sand contains more impurities, such as clay, silt, and organic matter. It is not much preferred because excessive extraction can lead to the depletion of natural resources.
However, River sand is more expensive due to the costs associated with mining, transporting, and legal restrictions. Hence, M Sand can be cheaper as it is locally produced and doesn’t incur high transportation costs.
Is P sand better than River Sand?
Indeed, P Sand is better than River Sand. P Sand is produced in a controlled environment where it does not disturb natural river ecosystems. It is made by crushing rocks in a sustainable way. As excessive mining of river sand can harm riverbeds and aquatic life, people are concerned about extraction and over-mining. Overall, P Sand is affordable and known for its quality and smoother finish for plastering.
FAQs
P Sand stands for Plaster Sand, which is used for plastering walls.
M Sand stands for Manufactured Sand, which is a substitute for river sand in construction.
M Sand (Manufactured Sand) is artificially produced by crushing rocks, while P Sand (Plaster Sand) is a finer, smoother variety of M Sand, specifically used for plastering purposes due to its fine texture.
P sand, also known as plastering sand, is a fine, well-graded sand used in the application of plaster, providing a smooth and even finish for walls and ceilings.