If you’re a construction professional, project manager, and engineer who are constantly under pressure to meet tight deadlines without compromising quality, Rapid Hardening Cement (RHC) offers a crucial advantage. RHC allows projects to progress faster, reducing downtime and accelerating schedules.
Whether you’re working on urgent road repairs, precast concrete production, or emergency construction, RHC delivers the quick setting and high early strength needed to keep your projects on track. In this blog, we’ll explore RHC in detail.
What is Rapid Hardening Cement?
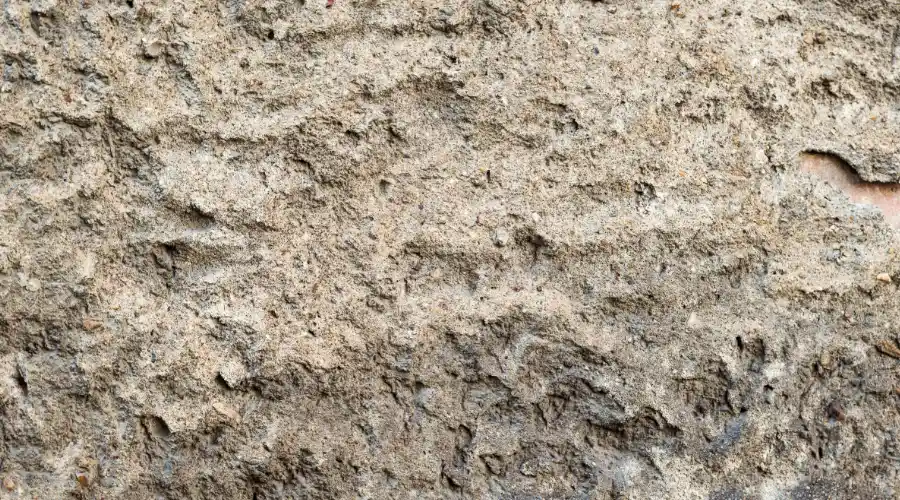
Rapid hardening cement is a unique type of cement with many added benefits. This cement is for construction professionals, like architects, engineers, and contractors. It’s also for disaster response teams and agencies in charge of fixing vital infrastructures.
Rapid hardening cement, also called high early strength cement, is a specific variety of cement. It gains strength much faster than Ordinary Portland Cement (OPC). It’s useful where early concrete strength is needed, such as in infrastructure repairs, after disasters, and with precast elements.
So, rapid hardening cement has a key difference from normal Portland cement. It has more tricalcium silicate (C3S), which is the compound that adds to early strength. Also, because the cement clinker is ground more thoroughly, RHC can reach the same strength as OPC in only 72 hours, whereas OPC takes 168 hours.
Manufacture of Rapid Hardening Cement
Making Rapid Hardening Cement involves a higher temperature process compared to making OPC. The blending of raw materials, such as limestone, clay, and other minerals required in the formulation of the cement, is done carefully to ensure the right chemical composition is obtained.
The process involves:
1. Grinding and Mixing: The raw materials are ground into a fine and uniform particle size and then blended to a required degree of uniformity.
2. Burning: The raw material is mixed and fed into a rotary kiln. It is then, burned at a higher temperature, typically around 1450°C, to form the cement clinker.
3. Grinding: The cement clinker is crushed and ground fine along with a moderate quantity of gypsum to act as a setting agent.
Composition of Rapid Hardening Cement
Rapid-hardening cement has more tricalcium silicate (C3S). It is usually 40% to 60% of the cement.
The other major components include:
– Dicalcium silicate (C2S): 15%
– Tricalcium aluminate (C3A): 10%
– Tetracalcium aluminoferrite (C4AF): 8%
The higher C3S content and the finer grinding of the cement are the key. They cause the rapid hardening and strength gain of the cement.
Properties of Rapid Hardening Cement
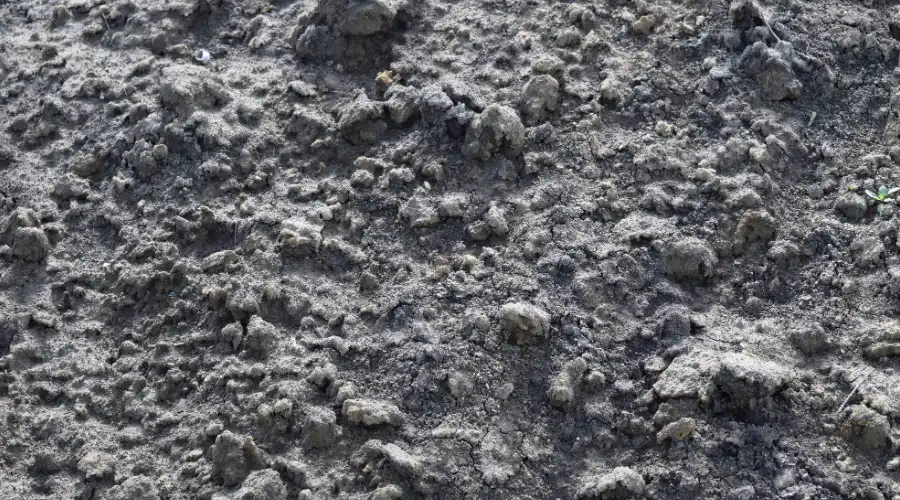
Strength Development
Rapid-hardening cement can develop strength at a much faster rate compared to OPC.
Setting Time
Rapid hardening cement’s initial setting time is 30 minutes and the final setting time is 600 minutes.
Early Strength Gain
Due to the higher C3S content, rapid hardening cement can achieve double the strength of OPC in the first 24 hours. It can reach the same 7-day strength as OPC in just 3 days.
Ultimate Strength
Early strength gain is much higher. However, the final strength of rapid-hardening cement is only slightly higher than OPC. It’s typically 10-20% greater.
Fineness
This cement has a higher specific surface area, over 3,250 cm²/g. This size makes it hydrate and harden faster.
Heat of Hydration
While being hydrated, the RH cement produces more heat than normal cement.
Shrinkage
The cement is ground to a higher fineness and has more C3S. This makes the product rapidly harden the cement. It shrinks less during curing and hardening than OPC.
Water Requirement
Rapid hardening cement uses a lower w/c ratio for set fluidity and strength. This is an added advantage compared to normal cement. It is due to better durability and less porosity.
Uses of Rapid Hardening Cement
Rapid hardening cement finds its primary applications in the following areas:
– Infrastructure construction and repair:
Works like roads, bridges, and any other structure need early strength. They cannot afford to wait for their strength to develop.
– Precast concrete elements:
The slabs, poles, and other members are precast and used in RCC structures. These structures need quick stripping from the form. These members are made using rapid hardening cement.
– Cold weather concreting:
Rapid hardening cement gains strength early, making it ideal for cold regions where normal cement does not gain enough strength.
– Disaster response:
Quick-setting cement is required in the rehabilitation of structures affected by natural disasters and any other calamities.
Advantages of Rapid Hardening Cement
The key advantages of using rapid-hardening cement include:
1. Faster construction timelines:
The rate of strength gained enables the construction formwork to be removed faster hence, enhancing the rate of construction completion.
2. Suitability for cold climates:
The rapid hardening cement is much better than ordinary cement. It works well in cold regions.
3. Durability and resistance:
Significantly, rapid-hardening cement may entail lower shrinkage and higher chemical resistance.
4. Versatility:
Rapid hardening cement works for most construction, not just infrastructures but also precast items.
Alternatives to Rapid Hardening Cement
Rapid hardening cement has many benefits. But, other cement types may be suitable for some applications.
1. Ordinary Portland Cement (OPC):
Thus, OPC can be used in cases when construction project deadlines do not affect the need for early strength.
2. Sulphate-Resisting Cement:
This is for structures exposed to high sulfate in the soil or water. They should use sulphate-resistant cement.
3. Low-Heat Cement:
In massive concrete placing, heat of hydration is an issue. Low-heat cement can be a solution.
4. Extra Rapid Hardening Cement:
Extra Rapid Hardening Cement is a special cement. It is made by grinding rapid hardening cement with calcium chloride. It can reach its 28-day strength in as early as three days.
Conclusion
As the construction industry progresses into the future, probably, the use of advanced and superior specialty cement such as rapid hardening cement will increase meaning that the advancement of this particular cement type will not stagnate.