We’ve all wondered about homes built 100 years ago and how they stand so strongly. The reason is that high-quality mortar was used in their construction. Those old homes were built with stones or mud using a sand and lime mixture as mortar. In modern construction, mortar mixtures have evolved to cater to various needs. Let’s explore the mortar systems used today to construct strong brick houses.
Understanding Mortar in Brick Construction
Let’s clear the confusion between mortar and concrete. Concrete is made by mixing aggregates, cement, and water, used to build bridges, roads, buildings, and foundations. This is unlike mortar— a combination of cement, sand, water, and sometimes lime.
Mortar mix acts as a glue to hold bricks or blocks together, and it is helpful in bricklaying and filling gaps.
Why is Mortar Important for Brick Houses?
Mortar is a must-have material in brick construction. Without it, bricks can’t stand together firmly. Mortar provides structural integrity and enhances appearance. Interestingly, the brick-and-mortar look has become a popular wall design and aesthetic appeal.
Mortar not only fills gaps but also provides compressive strength by uniting bricks. It prevents pest attacks, water passage and ensures weather resistance. Ultimately, mortar creates a solid structure.
Types of Mortar for Brick Houses
Mortar types are categorised into four main classes based on their composition, usage, and compressive strength:
1. Type N
2. Type S
3. Type M
4. Type O
In all four types, Portland cement, hydrated lime, and water are common in the mix, but the ratio of the mix varies.
Type N Mortar
- Proportion- 1 part cement, 1 part lime, 6 parts sand
- Type N mortar is widely used in construction. It offers medium strength and durability, making it ideal for above-ground structures like walls, windows, and roofs.
- Type N mortar is suitable for various climates and supports minimal loads.
Type S Mortar
- Proportion- 2 parts cement, 1 part lime, 9 parts cement
- For construction works below the ground structure and in earthquake-prone zones, high tensile bonds and resistance to pressures are necessary.
- Unlike Type N, Type S mortar achieves high compressive strength due to its unique composition.
- It is suitable for foundations, pathways, underfloor and parking areas.
- Type S mortar can resist external and internal pressures and therefore ensure structural integrity.
Type M Mortar
- Proportion- 3 parts cement, 1 part lime, 12 parts sand
- Type M mortar offers the highest compressive strength among all mortar types.
- It’s ideal for high-traffic areas, pavement, foundations, load-bearing walls, and structures in harsh climatic conditions.
- Type M mortar provides exceptional strength and durability.
- However, its high cement content reduces its binding nature, making it challenging to work with.
- Due to its thick texture and limited workability, it is difficult to handle.
Type O Mortar
- Proportion – 1 part cement, 2 parts lime, 9 parts sand
- Type O mortar is rich in lime content and provides very low compressive strength.
- It can be used to repair joint areas and refill gaps in bricks.
- Due to its low load-bearing capacity, Type O mortar is not suitable for above the ground structures or high-traffic areas.
- Instead, it’s perfect for interior work, including non-load bearing structures and walls that act as divisions.
Compressive Strength
Mortars are graded based on the minimum compressive strength they can achieve at the age of 28 days.
- Type M mortar’s compressive strength ranges from 17.2 to 17.5 N/mm². It is ideal for heavy-duty applications due to its highest compressive strength.
- Type S Mortar can reach 12.41 N/mm² of compressive strength after a setting period of 28 days. It is suitable for exterior purposes with high compression.
- Type N Mortar has moderate compressive strength of 5.17 N/mm². It is a general-purpose mortar for both interior and exterior walls with moderate strength.
- Type O mortar has the lowest compressive strength of 2.41 N/mm². It is suitable only for non-load bearing walls.
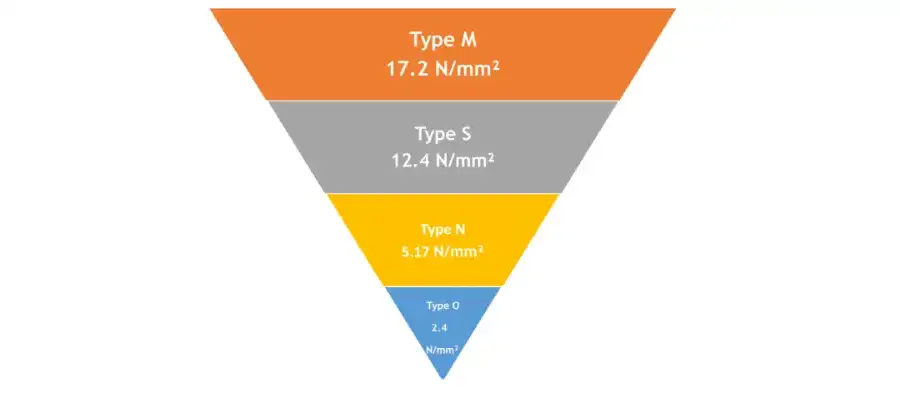
How to Choose the Right Mortar for Your Brick House
When choosing the mortar type for your brick house, several factors come into play. The number of storeys is a crucial consideration; for instance, single-storey buildings require less mortar strength, whereas multi-storey structures demand high-strength mortar, specifically Type M, in larger quantities.
Budget and proper planning are also vital to ensure sufficient funds for the project. Additionally, consider the environmental conditions, soil type, and project timeline to determine the most suitable mortar.
For outdoor spaces, such as sitting areas and parking, Type M mortar is ideal due to its high strength. In contrast, non-load bearing walls, slabs, and doors can utilise Type N mortar. Decorative portions like dwarf walls and cupboards, built for aesthetic appeal, are perfectly suited for Type O mortar.
Brick Type and Construction
Different brick types are available for homes, made from clay, concrete, or fly ash bricks. Each has its own strength and weakness. It is advisable to choose high-quality brick types based on your project. Burnt clay bricks are considered high-quality bricks for homes and are commonly used in many regions. However, they cost more than hollow blocks, typically used for load-bearing walls.
Moreover, the mortar system plays a crucial role in determining the bonding strength of bricks. Proper construction methods should be used when laying bricks. Nowadays, many tools have entered the market to speed up the bricklaying process.
There is always mortar waste during brick construction. However, experienced and trained labourers are skilled at minimising waste using specialised techniques and tools. Additionally, the thickness and level of mortar vary from brick to brick, depending on factors like brick size, shape, and texture. Bricks with hollows require more mortar, while dense bricks with a smoother texture need less.
Understanding the brick type, choosing the right mortar, and following proper construction methods can ensure the overall structural integrity and longevity of brick houses.
Climate and Environmental Considerations
Before starting your brick house construction, you should always keep in mind the climate and environmental factors. If the construction is going to take place in seismic zones, the mortar mix should have high compressive strength.
Regions near coastal areas face a major issue with saltwater. That will affect the bonding strength of mortar. Brick houses will start to crack in the future when mortar fails to do its role. Temperature conditions, and humidity levels will affect the setting time and strength of the mortar.
All kinds of environmental factors should be considered to prevent damages and cracks. By understanding these factors, following local guidelines, and choosing the right brick type, you can ensure the long-lasting building structures. This will reduce the maintenance and repair costs.
Tips for Applying Mortar for Brick House Construction
- First, clean the bricks and ensure they are free from dust and debris.
- Mix the mortar required for your project.
- Apply a uniform layer of mortar, approximately 1/4 inch thick.
- Hold the trowel at the correct angle to spread mortar uniformly.
- Move the tool in a zig-zag motion for full coverage.
- Place bricks and firm them tightly to avoid shifting.
- Fill joints and gaps between bricks with mortar using tools.
- Remove excess mortar.
- Allow 24 to 48 hours for the mortar to dry and set.
- The setting period takes around 28 days to achieve full strength.
How to Repair Mortar in a Brick Wall
Brick walls lose their bond or strength due to age, weather exposure, and water passage. Even with strong mortar, it degrades over time, causing cracks and breakages. It’s best to repair brick walls in the initial stages. This can be done by removing old mortar and applying new mortar. Follow these steps:
- Check for Damage: Look for signs of damage. Check if the brick wall has minor or deep cracks or significant water stains.
- Preparation: Prepare by buying the needed mortar mix and gathering the necessary tools. Clean the wall surface using a brush, cloth, or chisel.
- Remove Old Mortar: Carefully remove mortar from horizontal joint areas with a chisel. Insert the tool into the joints and gently scrape out the mortar, avoiding brick damage.
- Clean Joints: clean the joints using chisel, trowel or cloth.
- Prepare Surface: Mist the brick wall with water and let it absorb overnight.
- Mixing Mortar: Mix mortar in the correct ratio, following instructions.
- Fill Joints: Start horizontally, filling joints with mortar. Scoop mortar with your trowel, fill the required amount, then move to vertical joints. Use a sharp-edged tool to spread mortar.
- Allow to Set: the filled joints dry for a few days. Remove surface dust using a brush or cloth. Use a trowel to press and smooth the joints.
Important Tips
- Avoid adding excess mortar.
- Choose the correct mortar type.
- Let it dry for at least 48–72 hours.
Conclusion
It is clear from the above statements that choosing the right type of mortar is mandatory for constructing your home. It should align with environmental factors, budget, and personal preferences. For most residential brick homes, Type N mortar is often recommended due to its balance of strength and flexibility. However, for specific needs, such as structural integrity or exposure to harsh weather, consider using Type S or Type M mortar. Consider consulting with project experts to use mortar effectively and ensure the strength and safety of your home.
FAQs
The thickness of mortar for weight-bearing brick walls is typically a maximum of 3/8 inch. For other construction types, it can range from 1/8 inch to ¾ inch
Mortar typically takes 2-3 days to dry. The setting time varies based on climate factors. It usually takes 2-4 weeks to set completely.
Yes, different types of bricks require specific types of mortar for strong bonding and durability.